Semiconductor Metrology And Inspection Based On An X-Ray Source With An Electron Emitter Array
- Summary
- Abstract
- Description
- Claims
- Application Information
AI Technical Summary
Benefits of technology
Problems solved by technology
Method used
Examples
Example
[0042]Reference will now be made in detail to background examples and some embodiments of the invention, examples of which are illustrated in the accompanying drawings.
[0043]Methods and systems for realizing a high radiance x-ray source suitable for high throughput x-ray metrology and inspection based on a high density electron emitter array are presented herein. The high radiance x-ray source enables measurement of structural and material characteristics (e.g., material composition, dimensional characteristics of structures and films, defects, etc.) associated with different semiconductor fabrication processes.
[0044]In one aspect, a high radiance X-ray source includes an array of electron emitters that generate a large electron current focused over a small anode area to generate high radiance X-ray illumination light. In some embodiments, electron current density across the surface of the electron emitter array is at least 0.01 Amperes / mm2. Furthermore, the electron current is focus
PUM
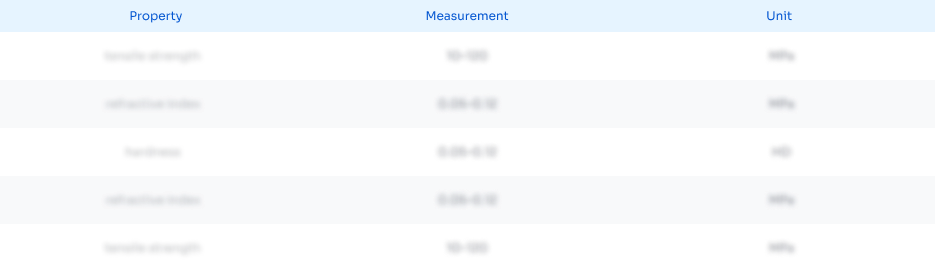
Abstract
Description
Claims
Application Information
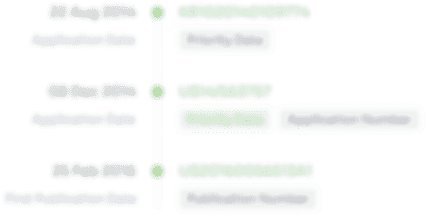
- R&D Engineer
- R&D Manager
- IP Professional
- Industry Leading Data Capabilities
- Powerful AI technology
- Patent DNA Extraction
Browse by: Latest US Patents, China's latest patents, Technical Efficacy Thesaurus, Application Domain, Technology Topic.
© 2024 PatSnap. All rights reserved.Legal|Privacy policy|Modern Slavery Act Transparency Statement|Sitemap