Preparing method of active methylene group modified waterborne polyurethane adhesive
A technology of active methylene and water-based polyurethane, which is applied in the direction of polyurea/polyurethane adhesives, adhesives, adhesive types, etc., can solve the problems of water resistance, poor chemical resistance, slow drying speed, etc., and achieve good Effects of water resistance, improved drying speed, and ease of industrial production
- Summary
- Abstract
- Description
- Claims
- Application Information
AI Technical Summary
Problems solved by technology
Method used
Examples
Example Embodiment
[0017] Example one:
[0018] Prepare the raw materials according to the following parts by mass: 30 parts of isophorone diisocyanate; 30 parts of polycaprolactone diol; 15 parts of DMPA; 15 parts of linoleic acid; 25 parts of dimethyl isophthalate-5-sodium sulfonate ; 35 parts of neoglutaric acid; 12 parts of trimethylolpropane; 0.2 parts of catalyst diethylbutyltin dilaurate;
[0019] Mix neoglutaric acid and dimethyl isophthalate-5-sodium sulfonate with stirring, heat to 230°C to react for 5h, cool to 180°C, add DMPA, continue to increase the temperature to 220°C, depressurize and dehydrate for 30min, get Water-soluble polyester polyol;
[0020] Mix linoleic acid and trimethylolpropane, add a catalyst, and react for 5 hours at 200°C under nitrogen flow to obtain active methylene oil;
[0021] The water-soluble polyester polyol and polycaprolactone diol are heated, mixed and stirred, dehydrated at 100°C and 200Pa vacuum for 1h, cooled to 50°C, added isophorone diisocyan
Example Embodiment
[0022] Embodiment two:
[0023] Prepare raw materials according to the following parts by mass: 40 parts of isophorone diisocyanate; 30 parts of polycaprolactone diol; 12 parts of DMPA; 20 parts of linoleic acid; 30 parts of dimethyl isophthalate-5-sodium sulfonate ; 40 parts of neoglutaric acid; 15 parts of trimethylolpropane; 0.1 part of catalyst diethylbutyltin dilaurate;
[0024] Mix neoglutaric acid and dimethyl isophthalate-5-sodium sulfonate with stirring, heat to 230°C to react for 5h, cool to 180°C, add DMPA, continue to increase the temperature to 220°C, depressurize and dehydrate for 30min, get Water-soluble polyester polyol;
[0025] Mix linoleic acid and trimethylolpropane, add a catalyst, and react for 5 hours at 200°C under nitrogen flow to obtain active methylene oil;
[0026] The water-soluble polyester polyol and polycaprolactone diol are heated, mixed and stirred, dehydrated at 100°C and 200Pa vacuum for 1h, cooled to 50°C, added isophorone diisocyanat
Example Embodiment
[0027] Embodiment three:
[0028] Prepare raw materials according to the following parts by mass: 50 parts of isophorone diisocyanate; 20 parts of polycaprolactone diol; 10 parts of DMPA; 10 parts of linoleic acid; 20 parts of dimethyl isophthalate-5-sodium sulfonate ; 35 parts of neoglutaric acid; 10 parts of trimethylolpropane; 0.5 parts of catalyst diethylbutyltin dilaurate;
[0029] Mix neoglutaric acid and dimethyl isophthalate-5-sodium sulfonate with stirring, heat to 230°C to react for 5h, cool to 180°C, add DMPA, continue to increase the temperature to 220°C, depressurize and dehydrate for 30min, get Water-soluble polyester polyol;
[0030] Mix linoleic acid and trimethylolpropane, add a catalyst, and react for 5 hours at 200°C under nitrogen flow to obtain active methylene oil;
[0031] The water-soluble polyester polyol and polycaprolactone diol are heated, mixed and stirred, dehydrated at 100°C and 200Pa vacuum for 1h, cooled to 50°C, added isophorone diisocya
PUM
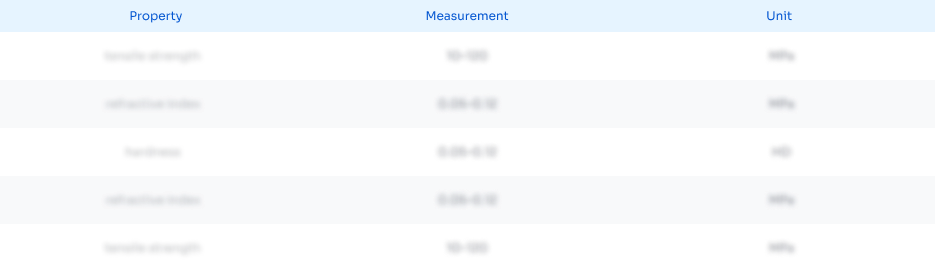
Abstract
Description
Claims
Application Information
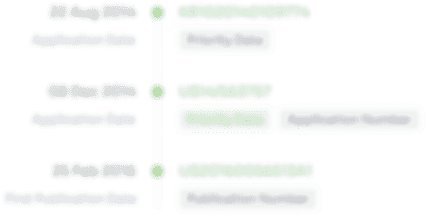
- R&D Engineer
- R&D Manager
- IP Professional
- Industry Leading Data Capabilities
- Powerful AI technology
- Patent DNA Extraction
Browse by: Latest US Patents, China's latest patents, Technical Efficacy Thesaurus, Application Domain, Technology Topic.
© 2024 PatSnap. All rights reserved.Legal|Privacy policy|Modern Slavery Act Transparency Statement|Sitemap