Antibacterial degradable vinylon and production method thereof
A production method, the technology of vinylon, applied in the field of vinylon, can solve the problems of secondary pollution, self-degradation, etc., achieve broad market development prospects, and reduce the risk of bacterial infection of patients
- Summary
- Abstract
- Description
- Claims
- Application Information
AI Technical Summary
Problems solved by technology
Method used
Image
Examples
Embodiment 1
[0022] Prepare spinning solution:
[0023] Polyvinyl alcohol 17-99 with a degree of polymerization of 1700-1800, boric acid and nano-complexed copper with a solid content of 10% are dissolved in hot water at 80°C to form a plastic chelate as a spinning solution; among them, polyvinyl alcohol The mass percentages of vinyl alcohol, boric acid, water and 10% solid content of nano-complex copper are 15%: 0.6%: 84.35%: 0.05%, respectively.
[0024] Coagulation spinning:
[0025] After the spinning solution is extruded through the spinneret, the sprayed spinning is coagulated in the alkaline coagulation bath formed by sodium sulfate and sodium hydroxide to obtain vinylon filaments; among them, the sodium sulfate and sodium hydroxide in the alkaline coagulation solution The dosages are 280g / L and 80g / L respectively, and the coagulation time is 8 seconds, so as to realize the dehydration and filamentation of vinylon fibers.
[0026] Oiling and Drying:
[0027] Mix the alcohol-solu
Embodiment 2
[0032] Prepare spinning solution:
[0033] Polyvinyl alcohol 17-99 with a degree of polymerization of 1700-1800, boric acid and nano-complex copper with a solid content of 9% are dissolved in hot water at 85°C to form a plastic chelate as a spinning solution; among them, poly The mass percentages of vinyl alcohol, boric acid, water and nano-complexed copper with a solid content of 9% are 17%: 0.7%: 82.22%: 0.08%, respectively.
[0034] Coagulation spinning:
[0035] After the spinning solution is extruded through the spinneret, the sprayed spinning is coagulated in the alkaline coagulation bath formed by sodium sulfate and sodium hydroxide to obtain vinylon filaments; among them, the sodium sulfate and sodium hydroxide in the alkaline coagulation solution The dosages are 290g / L and 90g / L respectively, and the coagulation time is 9 seconds, so as to realize the dehydration and filamentation of vinylon fibers.
[0036] Oiling and Drying:
[0037] Mix the alcohol-soluble viny
Embodiment 3
[0041] Prepare spinning solution:
[0042] Polyvinyl alcohol 17-99 with a degree of polymerization of 1700-1800, boric acid and nano-complexed copper with a solid content of 10% are dissolved in hot water at 90°C to form a plastic chelate as a spinning solution; among them, poly The mass percentages of vinyl alcohol, boric acid, water and nano-complex copper with 10% solid content are 18%: 0.8%: 81.1%: 0.1%, respectively.
[0043] Coagulation spinning:
[0044] After the spinning solution is extruded through the spinneret, the sprayed spinning is coagulated in the alkaline coagulation bath formed by sodium sulfate and sodium hydroxide to obtain vinylon filaments; among them, the sodium sulfate and sodium hydroxide in the alkaline coagulation solution The dosages are 300g / L and 100g / L respectively, and the coagulation time is 10 seconds, so as to realize the dehydration and filamentation of vinylon fibers.
[0045] Oiling and Drying:
[0046] Mix the alcohol-soluble vinylon
PUM
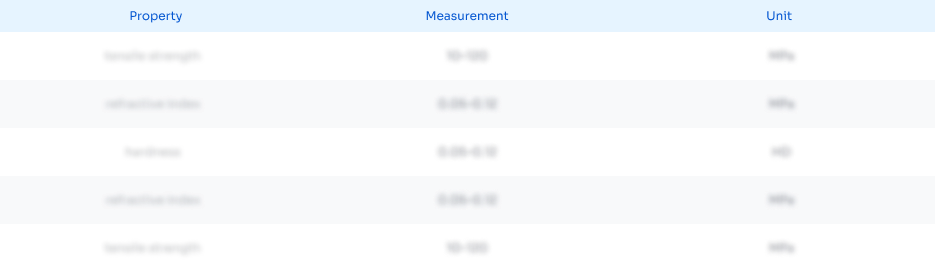
Abstract
Description
Claims
Application Information
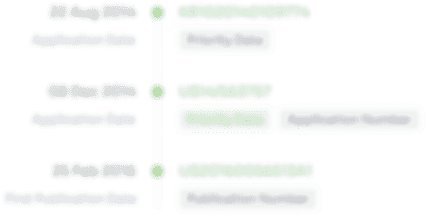
- R&D Engineer
- R&D Manager
- IP Professional
- Industry Leading Data Capabilities
- Powerful AI technology
- Patent DNA Extraction
Browse by: Latest US Patents, China's latest patents, Technical Efficacy Thesaurus, Application Domain, Technology Topic.
© 2024 PatSnap. All rights reserved.Legal|Privacy policy|Modern Slavery Act Transparency Statement|Sitemap