Method for preparing fuel oil by taking waste lubricating oil as raw material
A technology for waste lubricating oil and fuel oil, which is applied in the direction of lubricating compositions, petroleum industry, and hydrocarbon oil treatment, and can solve problems such as ecological environment damage, waste oil regeneration and use confusion, waste oil regeneration process backwardness, etc. pollution effect
- Summary
- Abstract
- Description
- Claims
- Application Information
AI Technical Summary
Benefits of technology
Problems solved by technology
Method used
Image
Examples
Embodiment 1
[0038] Distill the waste lubricating oil, collect the fraction between 300-500°C, and measure the density of the oil according to the national standard GB / T1884T2000 at 0.83-0.89g / cm 3 , the viscosity is measured according to the national standard GB / T2651998 between 2-11Mpa·s. Control the obtained fraction: water: the mass ratio of concentrated sulfuric acid is 60:35:5, stir and mix it well to form a mixed solution, heat the mixture to 60°C while stirring, and add sodium hydroxide to neutralize to pH 7 , stand still for 60 minutes to form an oil-water separation layer, the bottom is a waste water slag layer, and the upper part is a fuel oil layer. After removing the waste water slag layer at the bottom, the upper part is the recovery of fuel oil products.
[0039] The prepared fuel oil product is further distilled, and the fractions between 300-400°C are collected, and the fractions in this temperature range are added to the hydrofinishing catalyst reactor equipped with hi
Embodiment 2
[0041] Distill the waste lubricating oil, collect the fraction between 300-500°C, and measure the density of the oil according to the national standard GB / T1884T2000 at 0.83-0.89g / cm 3 , the viscosity is measured according to the national standard GB / T2651998 between 2-11Mpa·s. Control the obtained fraction: water: the mass ratio of concentrated sulfuric acid is 65:31:4, stir and mix it well to form a mixed solution, heat the mixture to 70°C while stirring, and add sodium hydroxide to neutralize to pH 7 , stand still for 70 minutes to form an oil and water separation layer, the bottom is a waste water slag layer, and the upper part is a fuel oil layer. After removing the waste water slag layer at the bottom, the upper part is the recovery of fuel oil products.
[0042] The prepared fuel oil product is further distilled, and the fractions between 300-400°C are collected, and the fractions in this temperature range are added to the hydrofinishing catalyst reactor equipped wit
Embodiment 3
[0044] Distill the waste lubricating oil, collect the fraction between 300-500°C, and measure the density of the oil according to the national standard GB / T1884T2000 at 0.83-0.89g / cm 3, the viscosity is measured according to the national standard GB / T2651998 between 2-11Mpa·s. Control the obtained fraction: water: the mass ratio of concentrated sulfuric acid is 70:28:2, stir and mix it well to form a mixed solution, heat the mixture to 75°C while stirring, and add sodium hydroxide to neutralize to pH 7 , standing still for 90min, forming oil and water separation layer, the bottom is the waste water slag layer, the upper part is the fuel oil layer, remove the waste water slag layer at the bottom, and the upper part is the fuel oil product recovery.
[0045] The prepared fuel oil product is further distilled, and the fractions between 300-400°C are collected, and the fractions in this temperature range are added to the hydrofinishing catalyst reactor equipped with high water
PUM
Property | Measurement | Unit |
---|---|---|
Viscosity | aaaaa | aaaaa |
Abstract
Description
Claims
Application Information
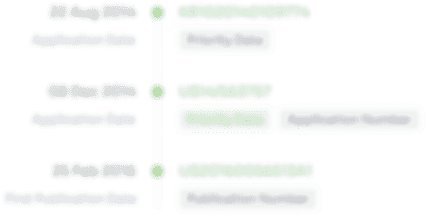
- R&D Engineer
- R&D Manager
- IP Professional
- Industry Leading Data Capabilities
- Powerful AI technology
- Patent DNA Extraction
Browse by: Latest US Patents, China's latest patents, Technical Efficacy Thesaurus, Application Domain, Technology Topic.
© 2024 PatSnap. All rights reserved.Legal|Privacy policy|Modern Slavery Act Transparency Statement|Sitemap