Advanced back side process fabrication method for improving IGBT performance
A technology of backside technology and manufacturing method, which is applied in semiconductor/solid-state device manufacturing, electrical components, circuits, etc., and can solve the problem that the concentration and depth of the N-type buffer layer are difficult to meet the requirements, the activation efficiency is not high, and the improvement of device performance is small, etc. problem, to achieve performance optimization, reduce power consumption, and reduce the size of the device
- Summary
- Abstract
- Description
- Claims
- Application Information
AI Technical Summary
Benefits of technology
Problems solved by technology
Method used
Image
Examples
Embodiment 1
[0052] The advanced back process manufacturing method for improving the performance of trench (Trench) gate field stop type IGBT in this embodiment, the steps are as follows:
[0053] (1) Carry out the front process of IGBT according to the conventional process
[0054] Prepare a piece of lightly doped substrate material with vapor phase doping or neutron irradiation, and select different doping concentrations or resistivities for the substrate material according to different withstand voltage requirements of IGBT devices. The front IGBT process is carried out on the substrate material. The main processes include: the production of the voltage-resistant ring and the field plate, the production of the Trench trench gate, the production of the conduction channel and the P-type collector layer, and the production of the emitter or source region. fabrication, fabrication of front contact holes, metal, passivation layers (eg figure 1 shown).
[0055] (2) After the front process is c
Embodiment 2
[0073] In this embodiment, the advanced backside process manufacturing method for improving the performance of the planar gate field termination type IGBT has the following steps:
[0074] (1) Carry out the front process of IGBT according to the conventional process
[0075] Prepare a piece of lightly doped substrate material with vapor phase doping or neutron irradiation, and select different doping concentrations or resistivities for the substrate material according to different withstand voltage requirements of IGBT devices. The front IGBT process is carried out on the substrate material. The main processes include: the production of the voltage-resistant ring and the field plate, the production of the planar gate, the production of the conduction channel and the P-type collector layer, and the production of the emitter or source region. , fabrication of front contact holes, metal, passivation layers (such as Figure 8 shown).
[0076] (2) After the front process is complete
PUM
Property | Measurement | Unit |
---|---|---|
Depth | aaaaa | aaaaa |
Depth | aaaaa | aaaaa |
Depth | aaaaa | aaaaa |
Abstract
Description
Claims
Application Information
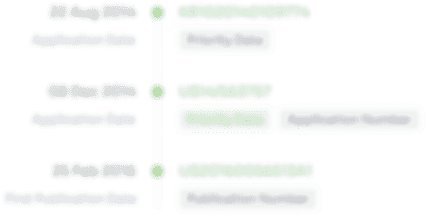
- R&D Engineer
- R&D Manager
- IP Professional
- Industry Leading Data Capabilities
- Powerful AI technology
- Patent DNA Extraction
Browse by: Latest US Patents, China's latest patents, Technical Efficacy Thesaurus, Application Domain, Technology Topic.
© 2024 PatSnap. All rights reserved.Legal|Privacy policy|Modern Slavery Act Transparency Statement|Sitemap