Method for improving double bulges at edge part of broadened intermediate slab in thick plate rolling process
A rolling process and rolling centerline technology, applied in the field of steel plate rolling, can solve the problems of increasing the amount of slab blanks, reducing the yield of finished steel plates, etc. Effect
- Summary
- Abstract
- Description
- Claims
- Application Information
AI Technical Summary
Benefits of technology
Problems solved by technology
Method used
Image
Examples
Embodiment Construction
[0024] The method for improving the double drums at the edge of the middle billet in the thick plate rolling process of the present invention will be further explained and illustrated in conjunction with the accompanying drawings and specific examples, but the following explanations and illustrations are not specific to the present invention The technical solution constitutes an improper restriction.
[0025] image 3 It shows the process steps in one embodiment of the method for improving the double drums at the edge of the middle billet in the thick plate rolling process described in the present invention.
[0026] Such as image 3 As shown, in this embodiment, taking a slab with a size of 400×1500×4600 (mm) as an example, its existing target size is 80×4430×7752 (mm), and the improved thick plate rolling of the present invention A method for widening the double drums at the edge of the middle billet during the manufacturing process, the steps comprising:
[0027] (A1) The b
PUM
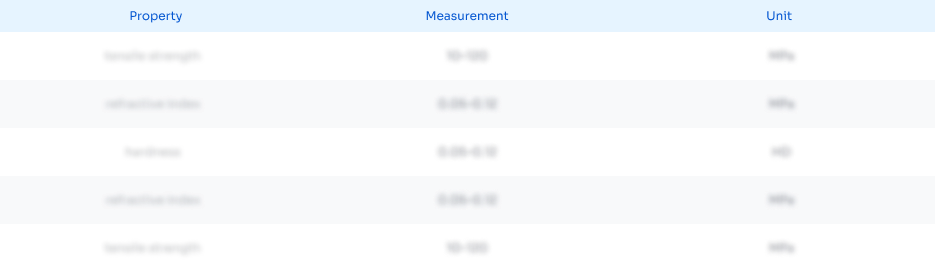
Abstract
Description
Claims
Application Information
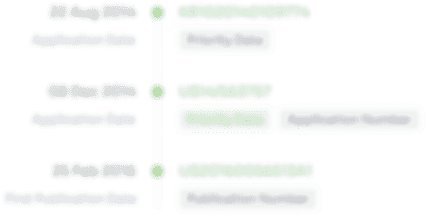
- R&D Engineer
- R&D Manager
- IP Professional
- Industry Leading Data Capabilities
- Powerful AI technology
- Patent DNA Extraction
Browse by: Latest US Patents, China's latest patents, Technical Efficacy Thesaurus, Application Domain, Technology Topic.
© 2024 PatSnap. All rights reserved.Legal|Privacy policy|Modern Slavery Act Transparency Statement|Sitemap