Dehydrogenation catalyst for light alkanes and preparation method thereof
A dehydrogenation catalyst, a technology for low-carbon alkanes, applied in the direction of hydrocarbons, hydrocarbons, molecular sieve catalysts, etc., can solve the problem of no industrialized examples of aerobic dehydrogenation technology, achieve good dehydrogenation activity and selectivity, reduce Effects of single pass life and olefin selectivity
- Summary
- Abstract
- Description
- Claims
- Application Information
AI Technical Summary
Problems solved by technology
Method used
Image
Examples
Embodiment 1
[0025] Preparation of the carrier: Select 200g of ZSM-5 molecular sieve with a relative crystallinity of 50% and a silicon-aluminum ratio of 100, mix them evenly with 350g of alumina and 25g of turnip powder, add 50g of dilute nitric acid solution with a mass concentration of 10%, knead and extrude forming. The molded carrier was dried in the shade for 24 hours, then dried in an oven at 110° C. for 12 hours, and then baked in a muffle furnace at 600° C. for 6 hours.
[0026]Loading of active components and additives: impregnate the calcined bar-shaped carrier with an aqueous solution containing an appropriate amount of chloroplatinic acid, tin tetrachloride and hydrochloric acid, then dry at 110°C for 4 hours, and then bake at 500°C for 4 hours. Then the catalyst was impregnated with an aqueous solution containing potassium nitrate, dried at 110°C for 4 hours, and calcined at 500°C for 4 hours. The percentage by weight of each elemental metal in the prepared catalyst to the carr
Embodiment 2
[0039] Preparation of the carrier: Select 200g of ZSM-5 molecular sieve with a relative crystallinity of 70% and a silicon-aluminum ratio of 100, mix them evenly with 350g of alumina and 25g of turnip powder, add 50g of dilute nitric acid solution with a mass concentration of 10%, knead and extrude forming. The molded carrier was dried in the shade for 24 hours, then dried in an oven at 110° C. for 12 hours, and then baked in a muffle furnace at 600° C. for 6 hours.
[0040] Loading of active components and additives: impregnate the calcined strip carrier with an aqueous solution containing appropriate amount of chloroplatinic acid, tin tetrachloride and hydrochloric acid, then dry at 110°C for 5 hours, and then bake at 500°C for 6 hours. The catalyst was impregnated with an aqueous solution containing potassium nitrate, dried at 110°C for 4 hours, and calcined at 500°C for 6 hours. The percentage by weight of each elemental metal in the prepared catalyst to the carrier is: Pt1w
Embodiment 3
[0042] Preparation of the carrier: Select 200g of ZSM-5 molecular sieve with a relative crystallinity of 60% and a silicon-aluminum ratio of 180, mix them evenly with 500g of alumina and 35g of turnip powder, add 80g of dilute nitric acid solution with a mass concentration of 8%, knead and extrude forming. The molded carrier was dried in the shade for 24 hours, then dried in an oven at 110° C. for 12 hours, and then baked in a muffle furnace at 600° C. for 6 hours.
[0043] Loading of active components and additives: impregnate the calcined bar-shaped carrier with an aqueous solution containing an appropriate amount of chloroplatinic acid, tin tetrachloride and hydrochloric acid, then dry at 110°C for 4 hours, and then bake at 500°C for 5 hours. Then the catalyst was impregnated with an aqueous solution containing potassium nitrate, dried at 110°C for 5 hours, and calcined at 500°C for 4 hours. The percentage by weight of each elemental metal in the prepared catalyst to the carr
PUM
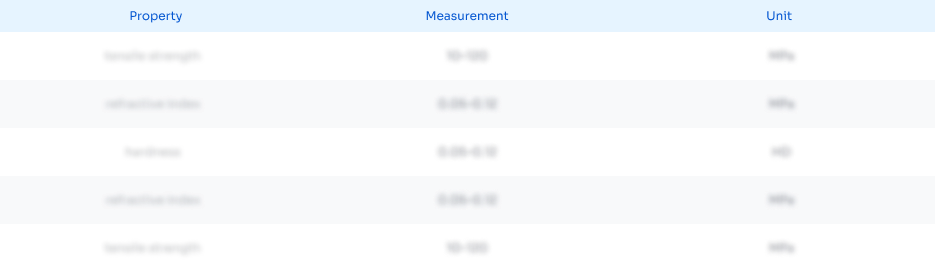
Abstract
Description
Claims
Application Information
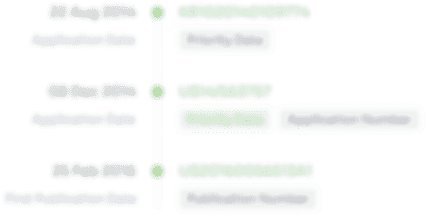
- R&D Engineer
- R&D Manager
- IP Professional
- Industry Leading Data Capabilities
- Powerful AI technology
- Patent DNA Extraction
Browse by: Latest US Patents, China's latest patents, Technical Efficacy Thesaurus, Application Domain, Technology Topic.
© 2024 PatSnap. All rights reserved.Legal|Privacy policy|Modern Slavery Act Transparency Statement|Sitemap