Method for preparing polyester fiber reinforced epoxy composite material based on chemical modification
A composite material and chemical modification technology, applied in the field of chemically modified polyester reinforced epoxy composite materials, can solve the problems of limited improvement, and achieve the effects of simple operation, improved interface bonding strength, and improved surface properties
- Summary
- Abstract
- Description
- Claims
- Application Information
AI Technical Summary
Problems solved by technology
Method used
Examples
specific Embodiment approach 1
[0010] Specific embodiment one: Grafting acrylamide on polyester fiber
[0011] Step 1: Boil the polyester fiber in a beaker for 15 minutes, extract it, and dry it for later use. Or degrease with ether in a beaker and dry it in an oven for half an hour before use.
[0012] Step 2: In a closed container or in a fume hood, soak the polyester fiber in the bulking agent-initiator solution at 80°C for 30 minutes, take it out and dry it. Proportion of puffing liquid: Add 5g of dibenzoyl peroxide, 40g of benzene monochloride and 10g of emulsifier (OP 10 ).
[0013] The third step: the grafting reaction is carried out in a 250ml three-necked flask, which is connected with stirring, a reflux condenser and a nitrogen inlet. The three-neck flask was placed in a super constant temperature water bath (T±0.5°C). Add acrylamide aqueous solution with a concentration of 16% into the bottle, pass nitrogen, keep the temperature constant, add the treated polyester fiber, react for a certain peri
specific Embodiment approach 2
[0015] Specific implementation mode two: Grafting acrylamide on polyester nonwoven fabric
[0016] Step 1: Boil the polyester nonwoven fabric in a beaker for 15 minutes, extract it, and dry it for later use. Or degrease with ether in a beaker and dry it in an oven for half an hour before use.
[0017] Step 2: In an airtight container or in a fume hood, soak the polyester nonwoven fabric in the bulking agent-initiator solution at 80°C for 30 minutes, take it out and dry it. Proportion of puffing liquid: Add 5g of dibenzoyl peroxide, 40g of benzene monochloride and 10g of emulsifier (OP 10 ).
[0018] The third step: the grafting reaction is carried out in a 250ml three-necked flask, which is connected with stirring, a reflux condenser and a nitrogen inlet. The three-neck flask was placed in a super constant temperature water bath (T±0.5°C). Add acrylamide aqueous solution with a concentration of 16% into the bottle, pass nitrogen, keep the temperature constant, add the treated
specific Embodiment approach 3
[0020] Specific embodiment three: Grafting acrylic acid on polyester fiber
[0021] Step 1: Weigh a certain amount of PET fiber, soak it in m-cresol for two hours at a temperature of 60°C, wash and air-dry;
[0022] The second step: the treated polyester fiber is mixed with a certain amount of 3.0×10 -3 mol / L KMnO 4 Put the solution together into the Erlenmeyer flask, inject nitrogen gas, and soak for 30 minutes at a constant temperature;
[0023] The third step: then add a certain amount of 0.02mol / L H 2 SO 4 With a small amount of 2.66mol / L acrylic acid (AA), a large amount of manganese dioxide precipitates are produced; after a certain amount of AA is added dropwise, react at a certain temperature for 2 hours to obtain grafted fibers.
[0024] Step 4: The modified PET fiber is dried for 15 minutes, and compounded with epoxy resin E-51 to prepare a composite material.
[0025] Embodiment 4: Grafting acrylic acid on polyester nonwoven fabric
[0026] Step 1: Weigh a
PUM
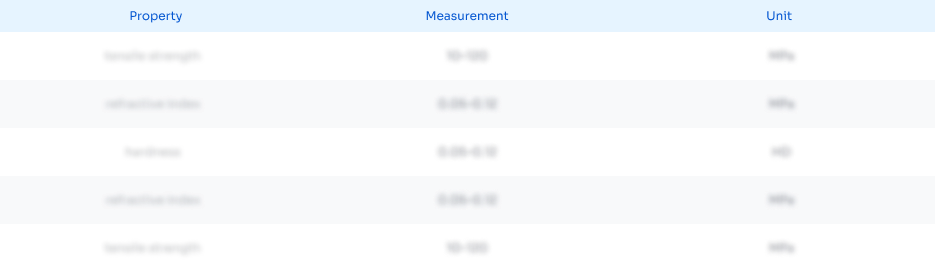
Abstract
Description
Claims
Application Information
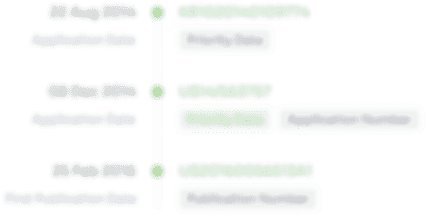
- R&D Engineer
- R&D Manager
- IP Professional
- Industry Leading Data Capabilities
- Powerful AI technology
- Patent DNA Extraction
Browse by: Latest US Patents, China's latest patents, Technical Efficacy Thesaurus, Application Domain, Technology Topic.
© 2024 PatSnap. All rights reserved.Legal|Privacy policy|Modern Slavery Act Transparency Statement|Sitemap