Pressure filling type cable former and cable forming process
A filling and cabling machine technology, applied in cable/conductor manufacturing, circuits, electrical components, etc., can solve problems such as reduced production efficiency, unrounded cable cores, inability to fill gaps, etc., to improve production efficiency and cable structure. Stable, densely packed effect
- Summary
- Abstract
- Description
- Claims
- Application Information
AI Technical Summary
Benefits of technology
Problems solved by technology
Method used
Image
Examples
Embodiment Construction
[0030] Such as figure 2 and image 3 As shown, the present invention discloses a pressure-filled cable forming machine, including a cable core pay-off frame 1, a paralleling mold 2, a calibrating mold 3, a filling device 4, a cooling device 5, a wrapping machine 6, a traction machine 7 and a wire take-up Machine 8. The cable core pay-off frame 1 is used to put the cable core, and the guide roller 9 and the line distribution plate 91 are arranged between the cable core pay-off frame 1 and the wire inlet of the parallel mold 2, and the wire outlet of the parallel mold 2 is connected with the shaping die. The line inlet 31 of 3 corresponds, and the filler inlet 33 of calibrating mold 3 is connected with the discharge port of filling device 4, and the wire outlet 32 of calibrating mold 3 is corresponding with the wire inlet of wrapping machine 6, and the wire outlet of calibrating mold 3 is connected with Cooling device 5 is arranged between the wire inlet of wrapping machine 6,
PUM
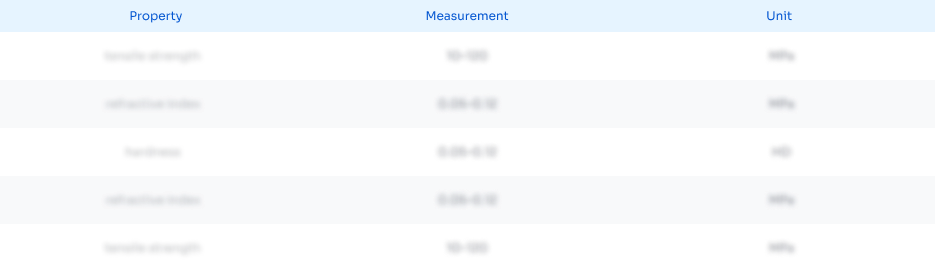
Abstract
Description
Claims
Application Information
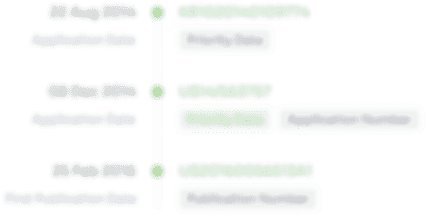
- R&D Engineer
- R&D Manager
- IP Professional
- Industry Leading Data Capabilities
- Powerful AI technology
- Patent DNA Extraction
Browse by: Latest US Patents, China's latest patents, Technical Efficacy Thesaurus, Application Domain, Technology Topic.
© 2024 PatSnap. All rights reserved.Legal|Privacy policy|Modern Slavery Act Transparency Statement|Sitemap