Monitoring method of internal stress of spacecraft composite material structure in aging process
A composite material and aging process technology, which is applied in the direction of measurement, instrumentation, and force measurement by measuring the change in optical properties of the material when it is stressed, can solve the problem of low resolution and the inability to achieve high resolution of the internal stress of the composite material structure Measurement and other issues, to achieve high spatial resolution, improve dimensional stability, and good repeatability
- Summary
- Abstract
- Description
- Claims
- Application Information
AI Technical Summary
Benefits of technology
Problems solved by technology
Method used
Image
Examples
Embodiment Construction
[0023] The present invention will be described in detail below in conjunction with specific embodiments. The following examples will help those skilled in the art to further understand the present invention, but do not limit the present invention in any form. It should be noted that those skilled in the art can make several modifications and improvements without departing from the concept of the present invention. These all belong to the protection scope of the present invention.
[0024] Such as figure 1 As shown, the method for monitoring the internal stress of the spacecraft composite structure aging process of the present invention comprises the following steps:
[0025] Step one, such as figure 2 As shown, carbon fiber prepreg 2, special optical fiber 3, carbon fiber prepreg 2, release cloth 5, and adhesive felt 6 are sequentially placed on the spacecraft composite structure forming mold 1, and the above carbon fiber prepreg 2, The special optical fiber 3, the carbon fi
PUM
Property | Measurement | Unit |
---|---|---|
Diameter | aaaaa | aaaaa |
Abstract
Description
Claims
Application Information
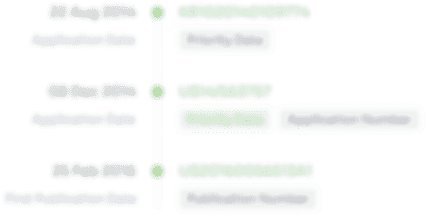
- R&D Engineer
- R&D Manager
- IP Professional
- Industry Leading Data Capabilities
- Powerful AI technology
- Patent DNA Extraction
Browse by: Latest US Patents, China's latest patents, Technical Efficacy Thesaurus, Application Domain, Technology Topic.
© 2024 PatSnap. All rights reserved.Legal|Privacy policy|Modern Slavery Act Transparency Statement|Sitemap