A retaining and clamping device for high-frequency circumferential small tenon blade vibration fatigue test and its use method
A vibration fatigue and clamping device technology, applied in vibration testing, measuring devices, testing of machine/structural components, etc., can solve the problems affecting the normal operation of vibration fatigue testing, difficulty in processing, damage to retention and clamping devices, etc. The effect of stable fixing, reducing processing difficulty and improving efficiency
- Summary
- Abstract
- Description
- Claims
- Application Information
AI Technical Summary
Problems solved by technology
Method used
Image
Examples
Example Embodiment
[0028] Example 1
[0029] In this embodiment, the structure of the retaining and clamping device for the vibration fatigue test of the high-frequency circumferential small tenon blade is as follows: Figure 4 , Figure 5 , Image 6 As shown, it is mainly composed of upper tightening bolt 1, force transmission retention strip 2, clamp 3, bracket 4, adapter plate 5, rear tightening bolt 6, rear tightening back cap 7 and auxiliary blade 8.
[0030] The tested blade 9 such as figure 1 , figure 2 As shown, the auxiliary blade 8 has the same shape and size as the tested blade 9; the adapter plate 5 is as Figure 4 , Figure 5 As shown, it is a circular plate body;
[0031] force transmission retaining strip 2 such as Figure 8 As shown, it includes a guide bar 2-1 and a top bar 2-2 that is an integrated structure with the guide bar, and one end of the force transmission and retention bar 2 is provided with a limit block 2-3, and the guide bar 2-1 and the top bar 2-2 are quadra
Example Embodiment
[0034] Example 2
[0035] This embodiment uses the retaining clamping device described in embodiment 1 to figure 1 , figure 2 The blade is clamped and fixed on an electromagnetic vibrating table for a vibration fatigue test. The operation is as follows:
[0036] ① Fix the adapter plate 5 on the surface of the electromagnetic vibration table with bolts, and then fix the fixture 3 on the adapter plate with bolts, and the center line of the fixture 3 coincides with the center line of the adapter plate 5;
[0037]②Fix the bracket 4 on the adapter plate 5 with bolts. The fixing position of the bracket 4 should be such that the fixture 3 is located under the top plate of the bracket 4 and the second screw hole set on the top plate, the tenon of the auxiliary blade and the tenon of the blade to be tested are installed in the fixture. The installation position on the clip body 3-2 corresponds;
[0038] ③Insert the force transmission retaining strip 2 into the groove cavity 3-2-1 prov
PUM
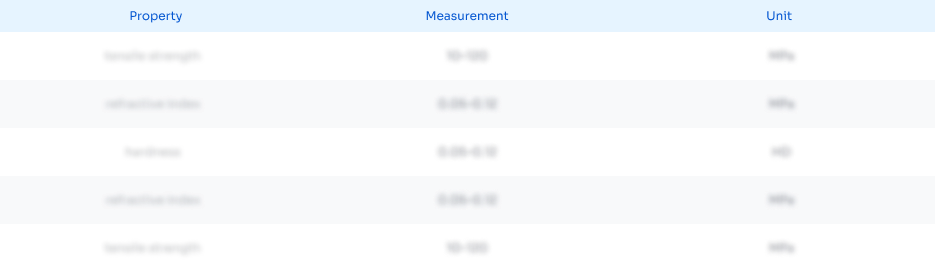
Abstract
Description
Claims
Application Information
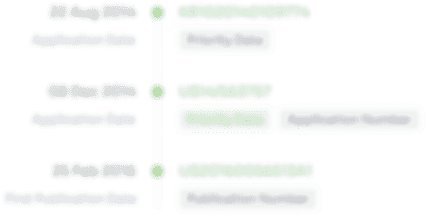
- R&D Engineer
- R&D Manager
- IP Professional
- Industry Leading Data Capabilities
- Powerful AI technology
- Patent DNA Extraction
Browse by: Latest US Patents, China's latest patents, Technical Efficacy Thesaurus, Application Domain, Technology Topic.
© 2024 PatSnap. All rights reserved.Legal|Privacy policy|Modern Slavery Act Transparency Statement|Sitemap