Method for preparing graphene by utilizing black-liquor rough lignin
A technology of lignin and graphene, applied in graphene, nano-carbon and other directions, can solve the problems of easy agglomeration, long sintering time, and uneven size of carbon source, and achieve the effect of reducing dosage, small size and reducing production cost.
- Summary
- Abstract
- Description
- Claims
- Application Information
AI Technical Summary
Problems solved by technology
Method used
Image
Examples
Example Embodiment
[0060] Example 1:
[0061] 1) The crude lignin extracted from the papermaking black liquor by acid deposition or electrolysis is used as raw material, crushed to below 80 mesh, and washed repeatedly with deionized water until the washing liquid is neutral.
[0062] 2) Centrifugal separation on a centrifuge at a speed of 4000 revolutions / min for 30 minutes, filter and separate the neutral crude lignin.
[0063] 3) The separated crude lignin is placed in a vacuum drying oven at 70° C. and dried to a moisture content of about 8%, and then ground into a powder with a particle size of less than 40 mesh.
[0064] 4) Weigh 8g of the above lignin powder, add 0.4g KOH and 40g deionized water to completely dissolve the lignin. After stirring for 0.5h in a magnetic stirrer, it was filtered, and the filtrate was placed in an evaporating dish and dried to absolute dryness at a temperature of 50°C to obtain a load K + 5g of alkali lignin is taken as the raw material for the preparation of graphene.
Example Embodiment
[0070] Example 2:
[0071] 1) The crude lignin extracted from the papermaking black liquor by acid deposition or electrolysis is used as raw material, crushed to below 80 mesh, and washed repeatedly with deionized water until the washing liquid is neutral.
[0072] 2) Centrifugal separation on a centrifuge at a speed of 4000 revolutions / min for 30 minutes, filter and separate the neutral crude lignin.
[0073] 3) The separated crude lignin is placed in a vacuum drying oven at 70° C. and dried to a moisture content of about 5%, and then ground into a powder with a particle size of less than 40 mesh.
[0074] 4) Weigh 8g of dried lignin powder, add 0.5g NaOH and 40g deionized water to completely dissolve the lignin. Stir in a magnetic stirrer for 1 hour and then filter. Place the filtrate in an evaporating dish and dry it to absolute dryness at 60°C to obtain a loaded Na + 5g of alkali lignin is taken as the raw material for the preparation of graphene.
[0075] 5) Configure the composite
Example Embodiment
[0080] Example 3:
[0081] 1) The crude lignin extracted from the papermaking black liquor by acid deposition or electrolysis is used as raw material, crushed to below 80 mesh, and washed repeatedly with deionized water until the washing liquid is neutral.
[0082] 2) Centrifugal separation on a centrifuge at a speed of 4000 revolutions / min for 30 minutes, filter and separate the neutral crude lignin.
[0083] 3) The separated crude lignin is placed in a vacuum drying oven at 70° C. and dried to a moisture content of about 5%, and then ground into a powder with a particle size of less than 40 mesh.
[0084] 4) Weigh 8g of dried lignin powder, add 0.75g KOH and 50g deionized water to completely dissolve the lignin. Stir in a magnetic stirrer for 1 hour and then filter. Place the filtrate in an evaporating dish and dry it to absolute dryness at 65°C to obtain a load K + 5g of alkali lignin is taken as the raw material for the preparation of graphene.
[0085] 5) The composite expansion ca
PUM
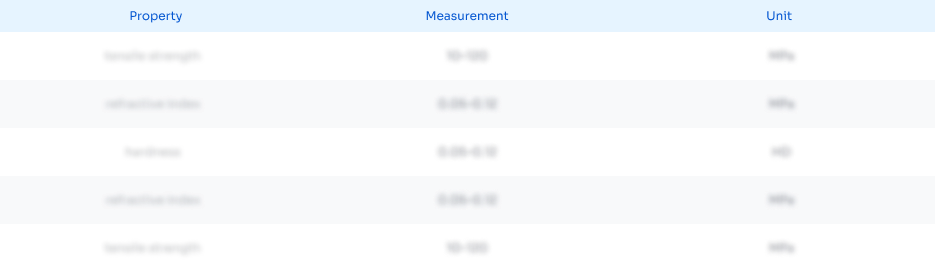
Abstract
Description
Claims
Application Information
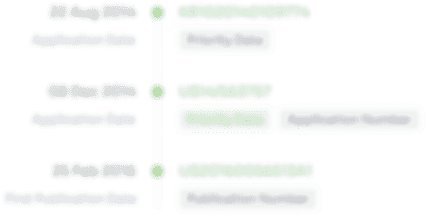
- R&D Engineer
- R&D Manager
- IP Professional
- Industry Leading Data Capabilities
- Powerful AI technology
- Patent DNA Extraction
Browse by: Latest US Patents, China's latest patents, Technical Efficacy Thesaurus, Application Domain, Technology Topic.
© 2024 PatSnap. All rights reserved.Legal|Privacy policy|Modern Slavery Act Transparency Statement|Sitemap