N-type single-sided cell preparation method
An N-type, single-sided technology, applied in the field of solar cells, can solve the problems of hindering the large-scale production of P-type cells, short lifespan of P-type silicon wafers, and low production efficiency, achieving low cost, low production efficiency, and uniform diffusion. Effect
- Summary
- Abstract
- Description
- Claims
- Application Information
AI Technical Summary
Benefits of technology
Problems solved by technology
Method used
Examples
Embodiment 1
[0025] A method for preparing an N-type single-sided battery, comprising the following steps:
[0026] 1) For N-type silicon chip texturing, the solution used for texturing is composed of the following components in weight percentage: 5% sodium hydroxide, 10% isopropanol, 1% silicon fluoride, and the balance is ammonia containing 3%wt ammonia;
[0027] 2) Use HCl solution with molar concentration of 5 mol / L, HF solution with 5 mol / L and HPO with 6 mol / L in sequence 3 solution cleaning;
[0028] 3) Preparation of POCl 3 mixed solution, the POCl 3 The mixed solution is composed of the following weight percentages: POCl 3 50%, HCl 5%, HPO 3 10%, V 2 o 5 0.5%, the balance is water;
[0029] 4) Paste SiO doped with 5% mass fraction on the back of the cleaned silicon wafer 2 the SiN mask, put the POCl 3 The mixture was placed in a diffusion furnace and heated at 300 °C for 60 minutes;
[0030] 5) Cool down, take out the silicon wafer after phosphorus diffusion, and
Embodiment 2
[0034] A method for preparing an N-type single-sided battery, comprising the following steps:
[0035] 1) For N-type silicon chip texturing, the solution used for texturing is composed of the following components in weight percentage: 10% sodium hydroxide, 15% isopropanol, 2% silicon fluoride, and the balance is ammonia containing 5%wt ammonia;
[0036] 2) Use HCl solution with molar concentration of 8 mol / L, HF solution with 10 mol / L and HPO with 8 mol / L in sequence 3 solution cleaning;
[0037] 3) Preparation of POCl 3 mixed solution, the POCl 3 The mixed solution is composed of the following weight percentages: POCl 3 70%, HCl 15%, HPO 3 20%, V 2 o 5 1%, the balance is water;
[0038] 4) Paste SiO doped with 10% mass fraction on the back of the cleaned silicon wafer 2 the SiN mask, put the POCl 3 The mixture was placed in a diffusion furnace and heated at 500°C for 30 min;
[0039] 5) Cool down, take out the silicon wafer after phosphorus diffusion, and clea
Embodiment 3
[0043] A method for preparing an N-type single-sided battery, comprising the following steps:
[0044] 1) For N-type silicon chip texturing, the solution used for texturing is composed of the following components in weight percentage: 5% sodium hydroxide, 10% isopropanol, 1% silicon fluoride, and the balance is ammonia containing 4%wt ammonia;
[0045] 2) Use HCl solution with molar concentration of 6 mol / L, HF solution with 8 mol / L and HPO with 7 mol / L in sequence 3 solution cleaning;
[0046] 3) Preparation of POCl 3 mixed solution, the POCl 3 The mixed solution is composed of the following weight percentages: POCl 3 60%, HCl 10%, HPO 3 15%, V 2 o 5 0.8%, the balance is water;
[0047] 4) Paste SiO doped with 8% mass fraction on the back of the cleaned silicon wafer 2 the SiN mask, put the POCl 3 The mixed solution was placed in a diffusion furnace and heated at 400°C for 45 minutes;
[0048] 5) Cool, take out the silicon wafer after phosphorus diffusion, an
PUM
Property | Measurement | Unit |
---|---|---|
Thickness | aaaaa | aaaaa |
Abstract
Description
Claims
Application Information
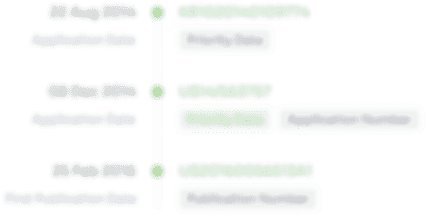
- R&D Engineer
- R&D Manager
- IP Professional
- Industry Leading Data Capabilities
- Powerful AI technology
- Patent DNA Extraction
Browse by: Latest US Patents, China's latest patents, Technical Efficacy Thesaurus, Application Domain, Technology Topic.
© 2024 PatSnap. All rights reserved.Legal|Privacy policy|Modern Slavery Act Transparency Statement|Sitemap