Preparation method of high-temperature-resistant epoxy resin adhesive
A technology of epoxy resin glue and high temperature resistance, applied in the direction of epoxy resin glue, adhesive, adhesive type, etc., can solve the problems of adhesive structure failure, easy cracking, poor high temperature resistance, etc., to improve temperature resistance Excellent performance and high temperature resistance, the effect of improving high temperature resistance
- Summary
- Abstract
- Description
- Claims
- Application Information
AI Technical Summary
Problems solved by technology
Method used
Examples
Example Embodiment
[0026] Example 1
[0027] Mix phenyltriethoxysilane with aluminum sulfate and n-butyl titanate at a mass ratio of 10:1:1 to obtain a mixture, and then mix the mixture with a 70% ethanol solution with a mass fraction of the mixture and put it into a reflux device In a three-necked flask, heated to 100°C, refluxed for 1 hour to obtain a metal-modified silicone resin; weighed the lilac flower petals into a pulverizer and pulverized for 1 hour to obtain a pulverized product. The pulverized product and petroleum ether were in a mass ratio of 1 : 10 After mixing, heat to 70℃, stir and extract with a magnetic stirrer at 300r / min for 3h; after the above-mentioned stirring and extraction, filter to remove the filter residue, separate the extract, put the extract into the distillation device, and distill and recover Petroleum ether to obtain the clove extract oil, the clove extract oil and the concentration is 10 6 The cfu / mL Pseudomonas aeruginosa suspension was mixed at a mass ratio of
Example Embodiment
[0028] Example 2
[0029] Mix phenyltriethoxysilane with aluminum sulfate and n-butyl titanate at a mass ratio of 10:1:1 to obtain a mixture, and then mix the mixture with a 70% ethanol solution with a mass fraction of it and put it into a reflux device In a three-necked flask, heated to 105℃, refluxed for 2h to obtain a metal modified silicone resin; weighed the lilac flower petals into a pulverizer and pulverized for 2h to obtain a pulverized product. The pulverized product and petroleum ether were mass ratio of 1 : 10 After mixing, heat to 75℃, stir and extract with a magnetic stirrer at 350r / min for 4h; after the above-mentioned stirring and extraction, filter to remove the filter residue, separate the extract, put the extract into the distillation device, and distill and recover Petroleum ether to obtain the clove extract oil, the clove extract oil and the concentration is 10 6 The cfu / mL Pseudomonas aeruginosa suspension was mixed at a mass ratio of 20:1 to obtain a fermen
Example Embodiment
[0030] Example 3
[0031] Mix phenyltriethoxysilane with aluminum sulfate and n-butyl titanate at a mass ratio of 10:1:1 to obtain a mixture, and then mix the mixture with a 70% ethanol solution with a mass fraction of it and put it into a reflux device In a three-necked flask, heated to 110℃, refluxed for 2h to obtain a metal modified silicone resin; weigh the lilac flower petals into a pulverizer and pulverize for 2h to obtain a pulverized product, and the pulverized product and petroleum ether by mass ratio of 1 : After mixing, heat to 80℃, stir and extract with a magnetic stirrer at 400r / min for 5h; after the above-mentioned stirring and extraction, filter to remove the filter residue, separate the extract, put the extract into the distillation device, and distill and recover Petroleum ether to obtain the clove extract oil, the clove extract oil and the concentration is 10 6 The cfu / mL Pseudomonas aeruginosa suspension was mixed at a mass ratio of 20:1 to obtain a fermentati
PUM
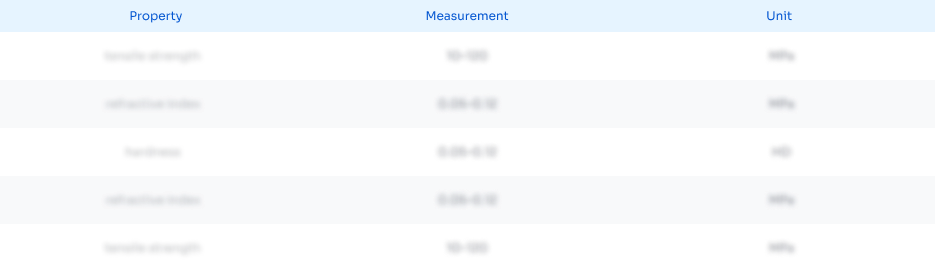
Abstract
Description
Claims
Application Information
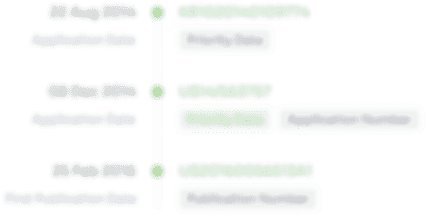
- R&D Engineer
- R&D Manager
- IP Professional
- Industry Leading Data Capabilities
- Powerful AI technology
- Patent DNA Extraction
Browse by: Latest US Patents, China's latest patents, Technical Efficacy Thesaurus, Application Domain, Technology Topic.
© 2024 PatSnap. All rights reserved.Legal|Privacy policy|Modern Slavery Act Transparency Statement|Sitemap