Method for preparing natural graphite radiating film from graphite oxide
A technology of natural graphite and heat-dissipating film, applied in the direction of graphite, etc., can solve the problems of increasing production difficulty, high price, and insignificant advantages of graphene in the washing process, and achieve the effect of excellent performance, easy washing and low cost.
- Summary
- Abstract
- Description
- Claims
- Application Information
AI Technical Summary
Benefits of technology
Problems solved by technology
Method used
Examples
Embodiment 1
[0022] Select 70 mesh flake graphite, and blend flake graphite with concentrated sulfuric acid and potassium permanganate in a mass ratio of 1:50:1. o After reacting at C for 1 h, the intercalated graphite obtained is blended with concentrated sulfuric acid and potassium permanganate in a ratio of 1:200:3 in mass ratio of flake graphite to concentrated sulfuric acid to potassium permanganate, 35 o C reacted for 5 hours, after washing, the graphite oxide was obtained by shaking in the aqueous solution to prepare a slurry with a concentration of 3 wt%, and coating it into a wet film with a thickness of 5 mm. o Dry film at C for 48 h to obtain dry film, dry film under the protection of high purity nitrogen 1000 o C carbonization treatment for 1 h, heating rate is 2 o C min -1 , After 10 o C min -1 To 3000 o C is graphitized for 3 h, and the resulting film is rolled at 5 MPa to be smooth.
[0023] The thickness of the natural graphite heat dissipation film obtained is 20 μm, and the in-pla
Embodiment 2
[0025] Select 70 mesh flake graphite, and blend flake graphite with concentrated sulfuric acid and potassium permanganate in a mass ratio of 1:50:1. o After reacting at C for 1 h, the intercalated graphite obtained is blended with concentrated sulfuric acid and potassium permanganate in a ratio of 1:200:3 by mass ratio of flake graphite to concentrated sulfuric acid to potassium permanganate, 35 o C reacted for 5 hours, after washing, the graphite oxide was obtained by shaking in the aqueous solution to prepare a slurry with a concentration of 3 wt%, and coating it into a wet film with a thickness of 5 mm. o Dry film at C for 48 h to get dry film, dry film at 90 o Soak in hydroiodic acid at C for 1 h, then at 10 o C min -1 To 3000 o C is graphitized for 3 h, and the resulting film is calendered at 5MPa to be smooth.
[0026] The thickness of the natural graphite heat dissipation film obtained is 22μm, and the in-plane thermal conductivity measured by the laser heat conduction method is
Embodiment 3
[0028] Select 150 mesh flake graphite, flake graphite and concentrated sulfuric acid and potassium permanganate are blended in a mass ratio of 1:50:1. o After reacting at C for 1 h, the intercalated graphite obtained is blended with concentrated sulfuric acid and potassium permanganate in a ratio of 1:200:3 by mass ratio of flake graphite to concentrated sulfuric acid to potassium permanganate, 35 o C reacted for 5 hours, after washing, the graphite oxide was obtained by shaking in the aqueous solution to prepare a slurry with a concentration of 3 wt%, and coating it into a wet film with a thickness of 5 mm. o Dry film at C for 48 h to obtain dry film, dry film under the protection of high purity nitrogen 1000 o C carbonization treatment for 1 h, heating rate is 2 o C min -1 , After 10 o C min -1 To 3000 o C is graphitized for 3 h, and the resulting film is rolled at 5 MPa to be smooth.
[0029] The thickness of the natural graphite heat dissipation film obtained is 20 μm, and the in-p
PUM
Property | Measurement | Unit |
---|---|---|
Thickness | aaaaa | aaaaa |
Thermal conductivity | aaaaa | aaaaa |
Conductivity | aaaaa | aaaaa |
Abstract
Description
Claims
Application Information
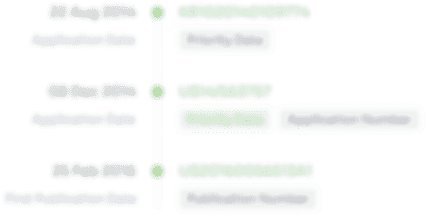
- R&D Engineer
- R&D Manager
- IP Professional
- Industry Leading Data Capabilities
- Powerful AI technology
- Patent DNA Extraction
Browse by: Latest US Patents, China's latest patents, Technical Efficacy Thesaurus, Application Domain, Technology Topic.
© 2024 PatSnap. All rights reserved.Legal|Privacy policy|Modern Slavery Act Transparency Statement|Sitemap