Preparation method for zeolite-activated carbon composite adsorbent
A composite adsorption and activated carbon technology, applied in chemical instruments and methods, alkali metal compounds, alkali metal oxides/hydroxides, etc., can solve the problem of low adsorption balance and separation, and achieve the effect of large adsorption capacity
- Summary
- Abstract
- Description
- Claims
- Application Information
AI Technical Summary
Benefits of technology
Problems solved by technology
Method used
Examples
Embodiment 1
[0018] The preparation method of zeolite-activated carbon composite adsorbent includes the following steps:
[0019] (1) According to the mass ratio of 1:3:2, mix coal gangue powder, pitch, and white carbon black, dry, and then carbonize in a tube furnace under nitrogen protection at a temperature of 1123K for 2 hours, and then pass in Carbon dioxide gas, then activated at 1123K for 24 hours to obtain the activated sample;
[0020] (2) Add the activated sample to a sodium hydroxide solution with a concentration of 4g / L, react at 338K for 12h, then stand still at room temperature for 12h, and then hydrothermally crystallize at 363K for 30h, and then use an ultrasonic power of 300W, Under the condition of ultrasonic frequency of 30Hz, ultrasonic dispersion for 30min, filtration, the filter residue was washed 5 times with deionized water, and then the filter residue was first dried at 80°C for 2h, and then dried at 105°C for 4h to obtain the zeolite-activated carbon composite material;
Embodiment 2
[0023] The preparation method of zeolite-activated carbon composite adsorbent includes the following steps:
[0024] (1) According to the mass ratio of 1:3:2, mix coal gangue powder, pitch, and white carbon black, dry, and then carbonize in a tube furnace under the protection of argon at a temperature of 1123K for 4 hours, and then pass Enter carbon dioxide gas, and then activate it at 1123K for 36 hours to obtain the activated sample;
[0025] (2) Add the activated sample to a sodium hydroxide solution with a concentration of 4g / L, react at 338K for 12h, then stand still at room temperature for 12h, and then hydrothermally crystallize at 363K for 24h, and then use an ultrasonic power of 200W, Under the condition of an ultrasonic frequency of 30 Hz, ultrasonic dispersion for 20 minutes, filtration, the filter residue was washed with deionized water 5 times, and then the filter residue was first dried at 80°C for 2 hours, and then dried at 105°C for 4 hours to obtain a zeolite-activa
Embodiment 3
[0028] The preparation method of zeolite-activated carbon composite adsorbent includes the following steps:
[0029] (1) According to the mass ratio of 1:3:2, mix coal gangue powder, pitch, and white carbon black, dry, and then carbonize in a tube furnace under the protection of argon at a temperature of 1123K for 3 hours, and then pass Enter carbon dioxide gas, and then activate it at 1123K for 28 hours to obtain an activated sample;
[0030] (2) Add the activated sample to a sodium hydroxide solution with a concentration of 4g / L, react at 338K for 12h, then stand still at room temperature for 12h, and then hydrothermally crystallize it at 363K for 28h, and then use an ultrasonic power of 300W, Under the condition of ultrasonic frequency of 30Hz, ultrasonic dispersion for 25min, filtration, the filter residue was washed 5 times with deionized water, and then the filter residue was first dried at 80°C for 2h, and then dried at 105°C for 4h to obtain the zeolite-activated carbon comp
PUM
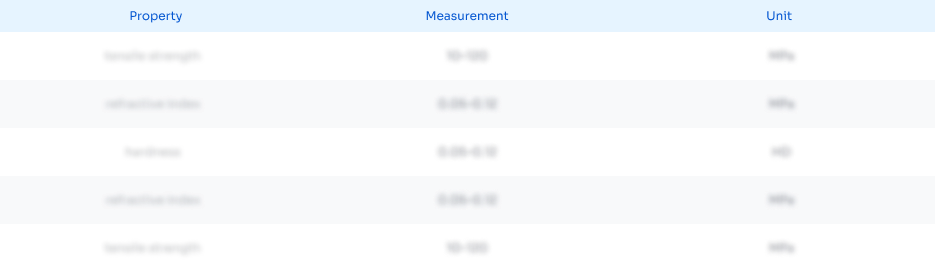
Abstract
Description
Claims
Application Information
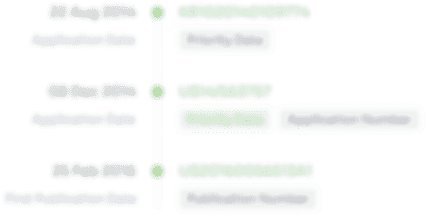
- R&D Engineer
- R&D Manager
- IP Professional
- Industry Leading Data Capabilities
- Powerful AI technology
- Patent DNA Extraction
Browse by: Latest US Patents, China's latest patents, Technical Efficacy Thesaurus, Application Domain, Technology Topic.
© 2024 PatSnap. All rights reserved.Legal|Privacy policy|Modern Slavery Act Transparency Statement|Sitemap