Silicon carbide micro-channel alkylation reactor and application method thereof
A technology of alkylation reactor and microchannel reaction, applied in chemical/physical/physical chemical reactors, chemical instruments and methods, chemical/physical/physical chemical processes, etc. Silicon carbide channel diameter is large, low conversion rate and other problems, to achieve the effect of low temperature alkylation reaction, high product quality, high octane number
- Summary
- Abstract
- Description
- Claims
- Application Information
AI Technical Summary
Benefits of technology
Problems solved by technology
Method used
Image
Examples
Embodiment 1~3
[0035] use as figure 1 The reactor of the shown structure uses sulfuric acid as a catalyst to carry out the alkylation reaction.
[0036] The molar ratio of isobutane to olefin is 3~10:1; the volume ratio of acid to hydrocarbon is 0.5~2:1; the residence time of the reaction material in the reactor is 1~30 min. The pressure at the bottom of the reactor is 0~0.05 MPa, and the pressure drop of the reactor is 0~0.4 MPa. The reaction temperature was maintained at -3~3°C.
[0037] The reactor structure is as follows: the diameter of the reactor is 50-300 mm, the height is 250-2500 mm, the height of the fiber bed is 10-120 mm, and the height of the silicon carbide bed is 100-1500 mm.
[0038] The specific reaction conditions are shown in Table 1, and the reaction results are shown in Table 2.
PUM
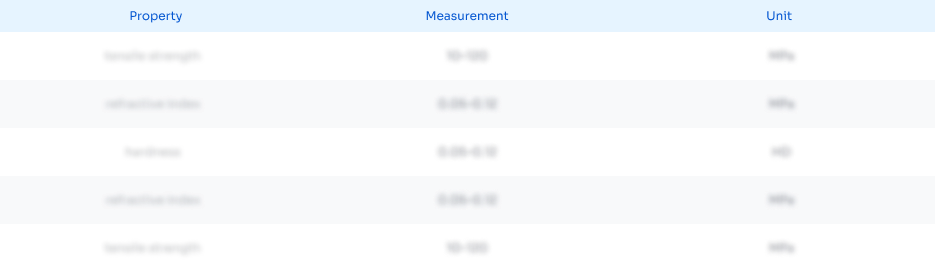
Abstract
Description
Claims
Application Information
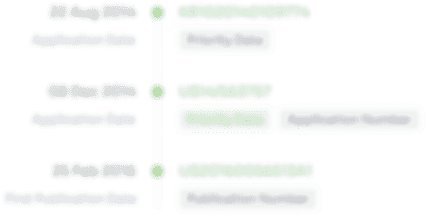
- R&D Engineer
- R&D Manager
- IP Professional
- Industry Leading Data Capabilities
- Powerful AI technology
- Patent DNA Extraction
Browse by: Latest US Patents, China's latest patents, Technical Efficacy Thesaurus, Application Domain, Technology Topic.
© 2024 PatSnap. All rights reserved.Legal|Privacy policy|Modern Slavery Act Transparency Statement|Sitemap