Aluminum alloy EBSD sample alkaline electrolysis polishing liquid and preparation method and electrolysis polishing method thereof
An electrolytic polishing and aluminum alloy technology, which is applied in the field of electrolytic polishing, can solve the problems of high equipment requirements for ion thinning method, damage to human body and environment, poor surface quality, etc., and achieve good polishing effect, less environmental pollution and good economic benefits. Effect
- Summary
- Abstract
- Description
- Claims
- Application Information
AI Technical Summary
Benefits of technology
Problems solved by technology
Method used
Image
Examples
Embodiment 1
[0028] In this embodiment, the composition of the alkaline electrolytic polishing solution is as follows: the content of sodium ethylate is 40 g / L, the content of sodium silicate is 15 g / L, the content of sodium metaaluminate is 10 g / L, and the content of glucose is 8 g / L .
[0029] The ZL205A alloy EBSD sample is electrolytically polished using the above-mentioned alkaline electrolytic polishing solution, and the steps of the electrolytic polishing method are as follows:
[0030] (1) Mechanical grinding and polishing: the ZL205A alloy material is made into semi-finished aluminum alloy samples by wire cutting, and the semi-finished aluminum alloy samples are sequentially used on the polishing machine with 800#, 1000#, 1500# and 2000# polishing sheets. Grinding, and then polishing with 0.1μm polishing paste;
[0031] (2) Degreasing treatment: the polished ZL205A alloy material obtained in (1) is degreased with a degreasing agent, and vibrated in an ultrasonic wave until t
Embodiment 2
[0035] In this embodiment, the composition of the alkaline electrolytic polishing solution is as follows: the content of sodium ethylate is 70g / L, the content of sodium silicate is 20g / L, the content of sodium metaaluminate is 15g / L, and the content of glucose is 10g / L , to obtain an electrolytic polishing solution after mixing evenly.
[0036] The ZL205A alloy EBSD sample was electrolytically polished using the above-mentioned alkaline electrolytic polishing solution, and the polishing process was the same as that in Example 1, but the polishing time was 140 s during electrolytic polishing.
[0037] After electropolishing, the surface of ZL205A alloy has high brightness and smooth surface. After EBSD analysis, the calibration rate is high. figure 2 It is the pattern diagram of EBSD image of ZL205A alloy after electrolytic polishing.
Embodiment 3
[0039] In this embodiment, the composition of the alkaline electrolytic polishing solution is as follows: the content of sodium ethylate is 100g / L, the content of sodium silicate is 25g / L, the content of sodium metaaluminate is 20g / L, and the content of glucose is 12g / L , to obtain an electrolytic polishing solution after mixing evenly.
[0040] The ADC12 alloy EBSD sample was electrolytically polished using the above-mentioned alkaline electrolytic polishing solution. The polishing process was the same as that in Example 1, but the polishing time was 3 minutes during the electrolytic polishing.
[0041] After electrolytic polishing, the surface of ADC12 alloy has high brightness and smooth surface. After EBSD analysis, the calibration rate is high. image 3 It is the pattern diagram of EBSD image of ADC12 alloy after electrolytic polishing.
[0042] In the above alkaline electrolytic polishing solution, sodium ethylate is the basic component, which is decomposed into et
PUM
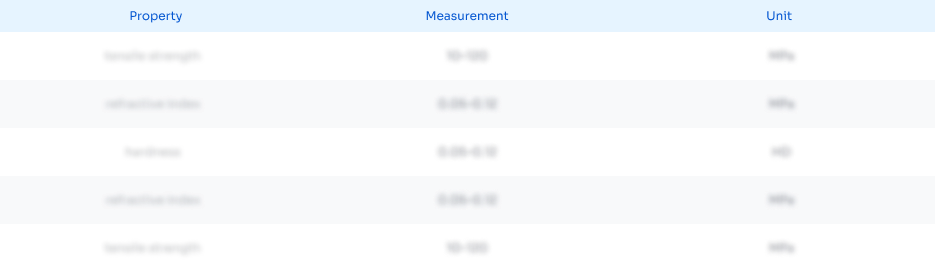
Abstract
Description
Claims
Application Information
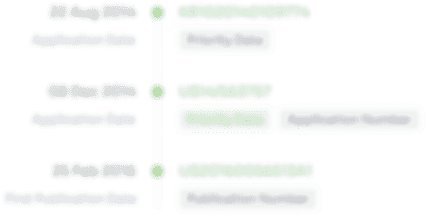
- R&D Engineer
- R&D Manager
- IP Professional
- Industry Leading Data Capabilities
- Powerful AI technology
- Patent DNA Extraction
Browse by: Latest US Patents, China's latest patents, Technical Efficacy Thesaurus, Application Domain, Technology Topic.
© 2024 PatSnap. All rights reserved.Legal|Privacy policy|Modern Slavery Act Transparency Statement|Sitemap