Phase-change-free heat-exchange integrated heating raw material coal water slurry gasification system and process
A technology of gasification system and coal water slurry, which is applied in the direction of gasification process, granular/powdered fuel gasification, chemical industry, etc. It can solve the problems of unusable low-grade steam heat, easy fouling and blockage of heat exchangers, and flash evaporation High equipment investment and other issues, to achieve the effect of improving energy utilization efficiency, improving system reliability and online rate, and reducing operation difficulty
- Summary
- Abstract
- Description
- Claims
- Application Information
AI Technical Summary
Problems solved by technology
Method used
Examples
Example Embodiment
[0038] Specific embodiments of the present invention will be described in detail below in conjunction with the accompanying drawings.
[0039] like figure 1 As shown, it is a schematic structural diagram of an integrated heating raw material coal-water slurry gasification system without phase change heat exchange, gasifier 1, scrubber 2, coal-water slurry / black water heat exchanger 5, gray water / black water exchanger The heater 6, the settling tank 3 and the gray water tank 4 are arranged in sequence and connected by pipelines. Among them, the coal water slurry / black water heat exchanger 5 and the gray water / black water heat exchanger 6 are all new non-fouling heat exchangers, and both choose shell-and-tube type non-fouling heat exchangers, and the internal exchange The heat pipes are corrugated elbows arranged in parallel, and the inner and outer surfaces of the elbows are coated with high-impact alumina ceramic coating. In the coal water slurry / black water heat excha
PUM
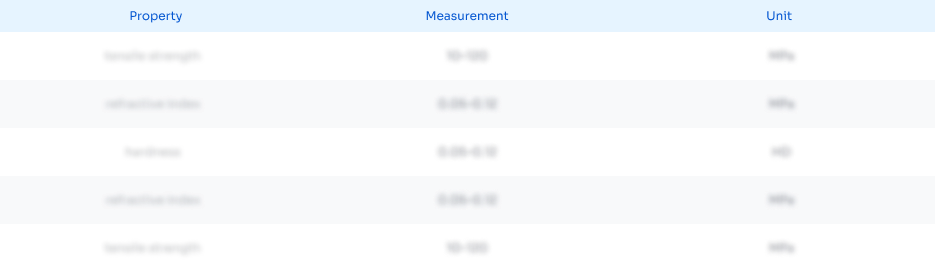
Abstract
Description
Claims
Application Information
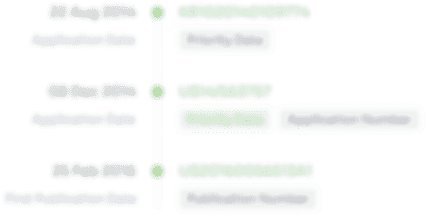
- R&D Engineer
- R&D Manager
- IP Professional
- Industry Leading Data Capabilities
- Powerful AI technology
- Patent DNA Extraction
Browse by: Latest US Patents, China's latest patents, Technical Efficacy Thesaurus, Application Domain, Technology Topic.
© 2024 PatSnap. All rights reserved.Legal|Privacy policy|Modern Slavery Act Transparency Statement|Sitemap