Graphene magnetic injection molding masterbatch for nylon electrical appliance plastics, and preparation method thereof
A technology of electrical plastics and graphene, applied in the field of plastic masterbatch, can solve the problems of poor compatibility, poor fluidity and magnetic properties, insufficient plastic and magnetic products to meet the shape, size, model, intelligence and other problems, and achieve melt flow. Good performance and improved dispersibility
- Summary
- Abstract
- Description
- Claims
- Application Information
AI Technical Summary
Benefits of technology
Problems solved by technology
Method used
Examples
Embodiment 1
[0029] (1) Add sulfonated graphene, iron salt and ferrous salt to deionized water, and prepare graphene-Fe by hydrothermal reaction in lye 3 o 4 Nanocomposite magnetic particles;
[0030] The iron salt is ferric chloride; the ferrous salt is ferrous chloride; the temperature of the hydrothermal reaction is 160°C, the pressure is 1.6MPa, and the time is 5h;
[0031] Wherein: 21 parts by weight of sulfonated graphene, 17 parts by weight of iron salt, 15 parts by weight of ferrous chloride, 62 parts by weight of deionized water;
[0032] (2) First, the graphene-Fe obtained in step (1) 3 o 4 Nanocomposite magnetic particles are surface treated with a coupling agent, then monocarboxyl-terminated nylon 6 and dispersant are added, mixed evenly, and then melted and extruded in an extruder to obtain a nylon 6 melt dispersed with nanocomposite magnetic particles; The coupling agent is isopropyl tris (dioctyl phosphate acyloxy) titanate; the dispersant is sodium methylene bis-naphthalen
Embodiment 2
[0037](1) Add sulfonated graphene, iron salt and ferrous salt to deionized water, and prepare graphene-Fe by hydrothermal reaction in lye 3 o 4 Nanocomposite magnetic particles;
[0038] The iron salt is ferric bromide; the ferrous salt is ferrous chloride; the temperature of the hydrothermal reaction is 150°C, the pressure is 1MPa, and the time is 7h;
[0039] Wherein: 20 parts by weight of sulfonated graphene, 16 parts by weight of iron salt, 15 parts by weight of ferrous chloride, 64 parts by weight of deionized water;
[0040] (2) First, the graphene-Fe obtained in step (1) 3 o 4 Nanocomposite magnetic particles are surface treated with a coupling agent, then monocarboxyl-terminated nylon 6 and dispersant are added, mixed evenly, and then melted and extruded in an extruder to obtain a nylon 6 melt dispersed with nanocomposite magnetic particles; The coupling agent is isopropyl dioleic acid acyloxy (dioctyl phosphate acyloxy) titanate; the dispersant is sodium methylene bi
Embodiment 3
[0045] (1) Add sulfonated graphene, iron salt and ferrous salt to deionized water, and prepare graphene-Fe by hydrothermal reaction in lye 3 o 4 Nanocomposite magnetic particles;
[0046] The iron salt is ferric sulfate; the ferrous salt is ferrous chloride; the temperature of the hydrothermal reaction is 170°C, the pressure is 2MPa, and the time is 5h;
[0047] Wherein: 22 parts by weight of sulfonated graphene, 19 parts by weight of iron salt, 14 parts by weight of ferrous chloride, 59 parts by weight of deionized water;
[0048] (2) First, the graphene-Fe obtained in step (1) 3 o 4 Nanocomposite magnetic particles are surface treated with a coupling agent, then monocarboxyl-terminated nylon 6 and dispersant are added, mixed evenly, and then melted and extruded in an extruder to obtain a nylon 6 melt dispersed with nanocomposite magnetic particles; The coupling agent is bis(dioctyloxypyrophosphate) ethylene titanate; the dispersant is sodium methylene bis-naphthalene sulfon
PUM
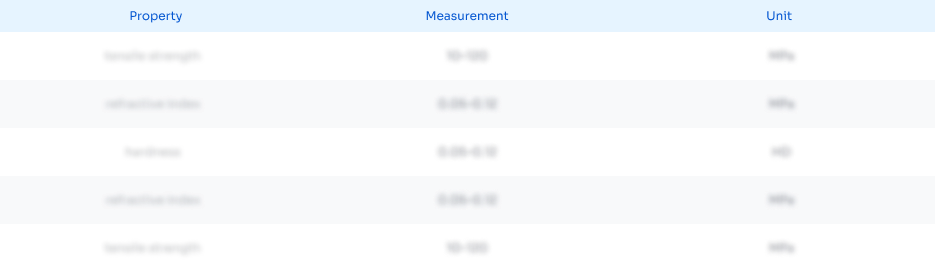
Abstract
Description
Claims
Application Information
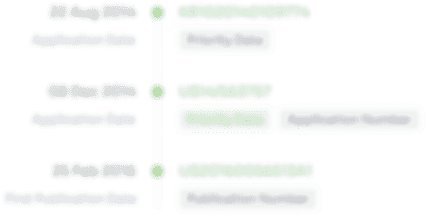
- R&D Engineer
- R&D Manager
- IP Professional
- Industry Leading Data Capabilities
- Powerful AI technology
- Patent DNA Extraction
Browse by: Latest US Patents, China's latest patents, Technical Efficacy Thesaurus, Application Domain, Technology Topic.
© 2024 PatSnap. All rights reserved.Legal|Privacy policy|Modern Slavery Act Transparency Statement|Sitemap