High-speed train grinding wheel and preparation method thereof
A grinding wheel and high-speed iron technology, which is applied in the direction of grinding/polishing equipment, grinding devices, manufacturing tools, etc., can solve the problems of service life, processing efficiency and poor yield of electroplated grinding wheels, and achieve low cost, improved service life, and good quality. The effect of holding power
- Summary
- Abstract
- Description
- Claims
- Application Information
AI Technical Summary
Problems solved by technology
Method used
Image
Examples
Example Embodiment
[0033] Example 1
[0034] This embodiment provides a method for preparing a high-speed iron grinding wheel. Including the following process steps:
[0035] 1) Ingredients: Pre-mix the graded diamond particles and silicon carbide particles with the alloy powder brazing filler metal to form a molding material. The mixing material uses a three-dimensional mixer and the mixing time is 50 minutes. The composition of the alloy powder brazing filler metal is 31wt% Ni, 25wt% Mn, 1.8wt% Si, 0.80wt% B, 1.0wt% Fe, 2.5wt% Cr, the balance being Cu; added diamond particles The weight of is 3.2wt% of the weight of the alloy powder solder, and the weight of the added silicon carbide particles is 0.40wt% of the weight of the alloy powder solder.
[0036] 2) Cloth: Adjust the tooling and mold, place the machined 65Mn steel substrate (after cleaning the surface of the steel substrate, pre-coated with adhesive and flow blocking agent), then put the molding material, and assemble it into the molding fixtu
Example Embodiment
[0042] Example 2
[0043] This embodiment provides a method for preparing a high-speed iron grinding wheel. Including the following process steps:
[0044] 1) Ingredients: Pre-mix the graded diamond particles and silicon carbide particles with the alloy powder brazing filler metal to form a molding material. The mixing material uses a three-dimensional mixer and the mixing time is 50 minutes. The composition of the alloy powder brazing filler metal is 35wt% Ni, 23wt% Mn, 2.0wt% Si, 0.80wt% B, 1.2wt% Fe, 3.2wt% Cr, the balance being Cu; added diamond particles The weight of is 2.5wt% of the weight of the alloy powder solder, and the weight of the added silicon carbide particles is 0.5wt% of the weight of the alloy powder solder.
[0045] 2) Cloth: Adjust the tooling and mold, place the machined 65Mn steel substrate (after cleaning the surface of the steel substrate, pre-coated with adhesive and flow blocking agent), then put in the molding material and assemble it into the molding fixt
Example Embodiment
[0051] Example 3
[0052] This embodiment provides a method for preparing a high-speed iron grinding wheel. Including the following process steps:
[0053] 1) Ingredients: Pre-mix the graded diamond particles and silicon carbide particles with the alloy powder brazing filler metal to form a molding material. The mixing material uses a three-dimensional mixer and the mixing time is 50 minutes. The composition of alloy powder brazing filler metal is 35wt% Ni, 24wt% Mn, 1.25wt% Si, 1.0wt% B, 1.5wt% Fe, 1.2wt% Cr, the balance being Cu; added diamond particles The weight of is 3.0wt% of the weight of the alloy powder solder, and the weight of the added silicon carbide particles is 0.3wt% of the weight of the alloy powder solder.
[0054] 2) Cloth: Adjust the tooling and mold, place the machined 65Mn steel substrate (after cleaning the surface of the steel substrate, pre-coated with adhesive and flow blocking agent), then put in the molding material and assemble it into the molding fixture.
PUM
Property | Measurement | Unit |
---|---|---|
Particle size | aaaaa | aaaaa |
Particle size | aaaaa | aaaaa |
Granularity | aaaaa | aaaaa |
Abstract
Description
Claims
Application Information
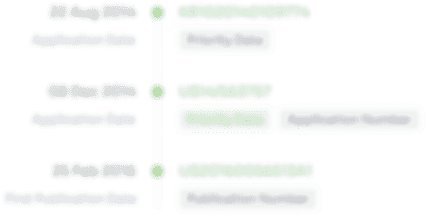
- R&D Engineer
- R&D Manager
- IP Professional
- Industry Leading Data Capabilities
- Powerful AI technology
- Patent DNA Extraction
Browse by: Latest US Patents, China's latest patents, Technical Efficacy Thesaurus, Application Domain, Technology Topic.
© 2024 PatSnap. All rights reserved.Legal|Privacy policy|Modern Slavery Act Transparency Statement|Sitemap