Supple crawling actuating mechanism
An actuating mechanism and compliant technology, applied in the directions of generator/motor, piezoelectric effect/electrostrictive or magnetostrictive motor, electrical components, etc. Compactness and other issues to achieve the effect of simple structure, fast response and easy processing
- Summary
- Abstract
- Description
- Claims
- Application Information
AI Technical Summary
Problems solved by technology
Method used
Image
Examples
Embodiment 1
[0045] When the present invention is powered on, the front clamping mechanism 1 and the rear clamping mechanism 3 are elongated by external excitation, and the front clamping claw 8 and the rear clamping claw 10 are clamped in the rigid guide rail 6, so that the crawling actuating mechanism is fixed on the rigid rail. Inside the guide rail 6, then reduce the voltage of the external excitation front clamping mechanism 1, the front clamping mechanism 1 shrinks, the front clamping claw 8 is separated from the rigid guide rail 6, and at the same time, the external excitation moves the telescopic mechanism 2, and the middle movement telescopic mechanism 2 stretches , the power-off clamping mechanism 5 breaks away from the rigid guide rail 6, and pushes the front clamping mechanism 1 to move forward. After the movement is completed, the voltage of the front clamping mechanism 1 is externally stimulated, the front clamping mechanism 1 is extended, and the front clamping claw 8 is engag...
Embodiment 2
[0047] When the present invention is powered on, the telescopic mechanism 2 is elongated, and the opening angle of the two transmission rods 12 becomes larger, so that the power-off clamping mechanism 5 is separated from the rigid guide rail 6, and the excitation voltage input during work is sometimes high and sometimes low, but It will not be lower than a certain amplitude, and the motion telescopic mechanism 2 expands and contracts with the excitation voltage, but it is always longer than the motion telescopic mechanism 2 in the initial state, so that the power-off clamping mechanism 5 will not be clamped on the rigid guide rail 6 wall, and the whole is compliant The crawling actuation mechanism can run smoothly. When the power is cut off, the motion telescopic mechanism 2 is in the initial state, and the power-off clamping mechanism 5 is clamped on the rigid guide rail 4 .
PUM
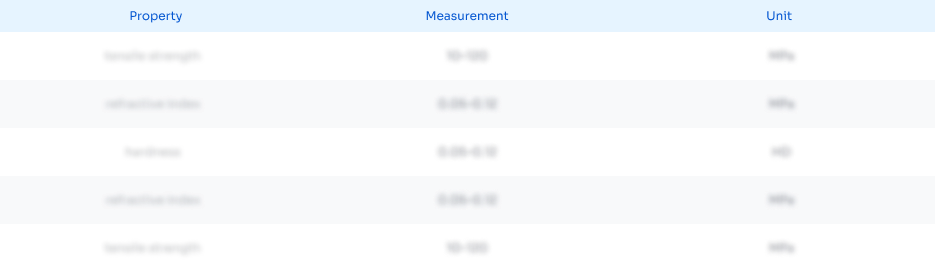
Abstract
Description
Claims
Application Information
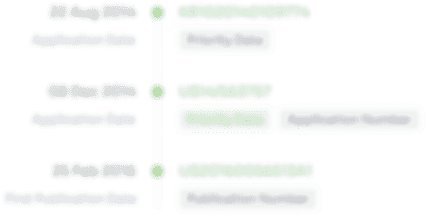
- R&D Engineer
- R&D Manager
- IP Professional
- Industry Leading Data Capabilities
- Powerful AI technology
- Patent DNA Extraction
Browse by: Latest US Patents, China's latest patents, Technical Efficacy Thesaurus, Application Domain, Technology Topic.
© 2024 PatSnap. All rights reserved.Legal|Privacy policy|Modern Slavery Act Transparency Statement|Sitemap