Grinding equipment for direct current (DC) plug plating layer
A plug and coating technology, applied in the field of DC plug coating grinding equipment, can solve the problems of inaccurate grinding position positioning, defective products, poor soldering, etc., and achieve the effect of avoiding pollution and high degree of automation
- Summary
- Abstract
- Description
- Claims
- Application Information
AI Technical Summary
Benefits of technology
Problems solved by technology
Method used
Image
Examples
Embodiment Construction
[0018] A kind of DC plug coating grinding equipment proposed by the present invention, such as figure 1 and figure 2 Shown, comprise: main frame 100 and vibrating plate frame 200 that are arranged side by side; Vibrating plate frame 200 is provided with feeding vibrating plate 300, and main frame 100 is provided with feeding mechanism 400, and the feeding end of feeding mechanism 400 and The feeding vibrating plate 300 is connected, and a material clamping translation mechanism 500 is provided outside the discharge end of the feeding mechanism 400, and a grinding mechanism 600 is provided above the material clamping translation mechanism 500; the grinding mechanism 600 includes: figure 2 Shown spindle motor 610, arbor 620, grinding tungsten steel blade (not shown), sliding support plate 640, two support vertical plates 650, linear guide rail fixing plate 660, linear guide rail 670, adjusting differential head 680, Separate the fixed plate 690 and the tension spring 691; two su
PUM
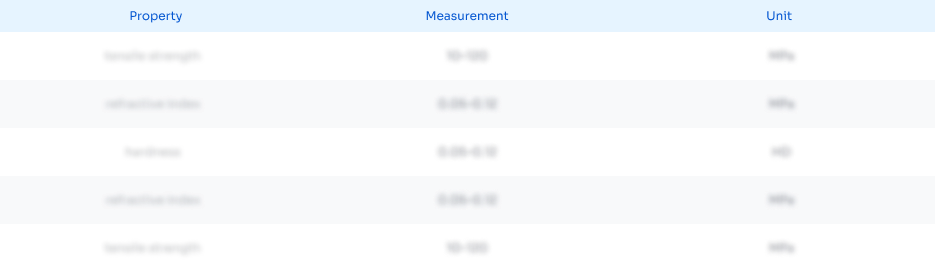
Abstract
Description
Claims
Application Information
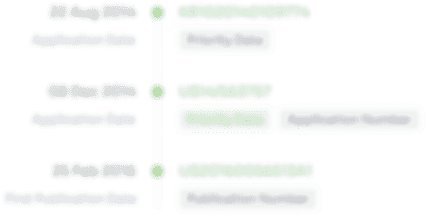
- R&D Engineer
- R&D Manager
- IP Professional
- Industry Leading Data Capabilities
- Powerful AI technology
- Patent DNA Extraction
Browse by: Latest US Patents, China's latest patents, Technical Efficacy Thesaurus, Application Domain, Technology Topic.
© 2024 PatSnap. All rights reserved.Legal|Privacy policy|Modern Slavery Act Transparency Statement|Sitemap