Excavator hydraulic control system and method
A hydraulic control system, hydraulic system technology, applied in mechanical equipment, fluid pressure actuating devices, servo motors, etc., can solve the problems of energy loss, large energy loss, poor economy, etc., and achieve the effect of solving energy loss
- Summary
- Abstract
- Description
- Claims
- Application Information
AI Technical Summary
Benefits of technology
Problems solved by technology
Method used
Image
Examples
Embodiment 1
[0040]A hydraulic control system for an excavator, comprising a LUDV load sensing valve 1, a control unit 4, a hydraulic oil tank 8, a preset number of gear pumps, and a two-position three-way electric control valve corresponding to the gear pumps one by one; the two-position three-way The oil inlet port of the electric control valve is connected to the oil outlet port of the corresponding gear pump, and the two oil outlet ports of the two-position three-way electric control valve are respectively connected to the oil inlet port of the LUDV load sensing valve and the system return port. The oil circuit (that is, connected to the hydraulic oil tank), each two-position three-way electric control valve is respectively connected with the control unit, the LS hole of the LUDV load sensing valve is connected with a pressure sensor 3, and the pressure sensor 3 is connected with the control unit 4, The control unit 4 controls the two-position three-way electric control valve in three stag
Embodiment 2
[0070] A hydraulic control method for an excavator, in which a LUDV load sensing valve, a control unit, a preset number of gear pumps, and two-position three-way electric control valves corresponding to the gear pumps are set in the hydraulic system; the two-position three-way electric control valve The oil inlet of the control valve is connected to the oil outlet of the corresponding gear pump, and the two oil outlets of the two-position three-way electric control valve are respectively connected to the oil inlet of the LUDV load sensing valve and the oil return of the system. Each two-position three-way electric control valve is connected to the control unit, and the LS hole of the LUDV load sensing valve is connected to a pressure sensor, which is connected to the control unit. The control unit controls the two-position three-way Electric control valve for control:
[0071] Stage I: From the initial working of the hydraulic system until the pressure detected by the pressure se
PUM
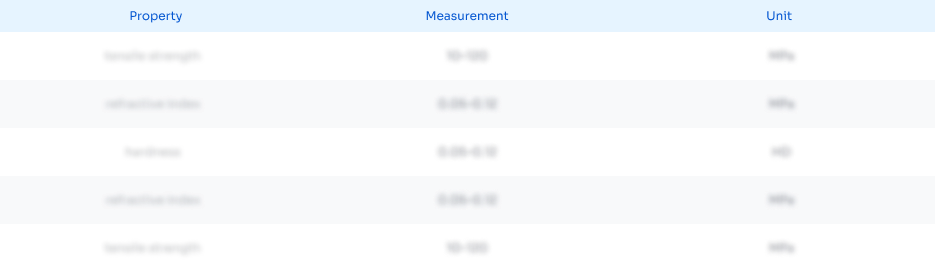
Abstract
Description
Claims
Application Information
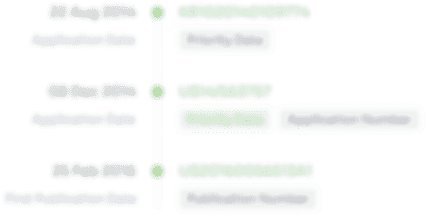
- R&D Engineer
- R&D Manager
- IP Professional
- Industry Leading Data Capabilities
- Powerful AI technology
- Patent DNA Extraction
Browse by: Latest US Patents, China's latest patents, Technical Efficacy Thesaurus, Application Domain, Technology Topic.
© 2024 PatSnap. All rights reserved.Legal|Privacy policy|Modern Slavery Act Transparency Statement|Sitemap