Cold plate optimization design method for heat dissipation of large-size flexible printed circuit board
A flexible printing and optimized design technology, applied in CAD circuit design, calculation, image data processing, etc., can solve problems such as difficulty in bonding printed boards and cold plates, temperature rise of heat source devices, thermal deformation of printed boards, etc. , to achieve the effect of increasing complexity, reducing contact thermal resistance, and satisfying heat dissipation
- Summary
- Abstract
- Description
- Claims
- Application Information
AI Technical Summary
Problems solved by technology
Method used
Examples
Example Embodiment
[0030] Embodiment 1: A cold plate optimization design method for heat dissipation of large-size flexible printed boards, including the following steps:
[0031] Step 1: Measure the coordinate values of n points on the printed board. The n points are mainly distributed around the heat source device, and the number n is not less than 100. The coordinate values (xi, yi, zi) of each point can be passed through the coordinate system Or measured by a laser scanner, draw a three-dimensional model using three-dimensional software based on the coordinate values of n points, and import the wiring distribution model of the printed board and the heat source device model into the three-dimensional model to form the initial state model of the printed board; the heat source device The number can be set by yourself. In this embodiment, the heat source devices are three types: CPU with high power consumption, network chip with medium power consumption, and power conversion module with low power
Example Embodiment
[0035] Embodiment 2: Different from embodiment 1, after step 3, there is also step 4: calculating the temperature difference △T between the heat source device and the cold plate in step 3, the △T calculation formula is: (L_power / (K_power*S_power) + L_tim / (K_tim*S_tim))*W, where L stands for distance, S stands for contact area, K stands for thermal conductivity, subscript power stands for heat source, subscript tim stands for heat transfer medium, and then according to the temperature difference △T and the allowable value of the heat source device Use the temperature T_max to calculate the surface temperature T_cp of the cold plate at different positions. The calculation formula is T_max – △T. The cold plate runner is designed to optimize the cold plate runner according to the temperature T_cp of the cold plate. The cold plate runner preferentially adopts a combination of multiple enhanced heat exchange runners , It is beneficial for more reasonable heat exchange and cold plate
Example Embodiment
[0040] Embodiment 3: Different from Embodiment 2, the optimization method of the cold plate runner in step 4 also includes step 4.4: Calculate the cold plate runner flow resistance P, and compare it with the flow resistance requirements proposed by the user. The formula for calculating the flow resistance P of the cold plate runner is: , Where P represents the flow resistance, n1~5 represents the number of the above five kinds of flow channels, and Q represents the flow. This step further optimizes the internal flow channel of the cold plate to meet the flow resistance P requirements of some users.
PUM
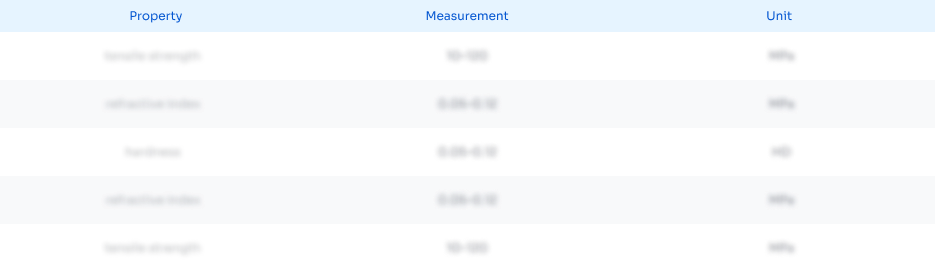
Abstract
Description
Claims
Application Information
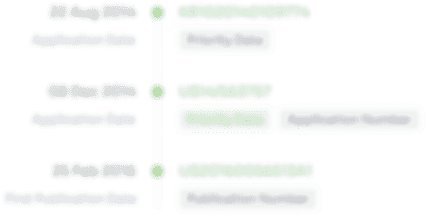
- R&D Engineer
- R&D Manager
- IP Professional
- Industry Leading Data Capabilities
- Powerful AI technology
- Patent DNA Extraction
Browse by: Latest US Patents, China's latest patents, Technical Efficacy Thesaurus, Application Domain, Technology Topic.
© 2024 PatSnap. All rights reserved.Legal|Privacy policy|Modern Slavery Act Transparency Statement|Sitemap