Rudder blade supporting frame and rudder blade mounting trolley
A technology for installing trolleys and supporting frames, which is applied in the directions of lifting devices, hoisting devices, ships, etc., which can solve the problems of low construction efficiency and large potential safety hazards.
- Summary
- Abstract
- Description
- Claims
- Application Information
AI Technical Summary
Benefits of technology
Problems solved by technology
Method used
Image
Examples
Embodiment 1
[0071] Figure 1 to Figure 4 Shown is a rudder blade support frame 10, which includes: a fixed frame 100, two first drivers 210, two groups of first pulley assemblies 220, a first moving frame 230 and a plurality of first flexible cables 240. The fixed frame 100 has a vertical channel (not shown) through which the top penetrates, and the fixed ends of the two first drivers 210 are fixed on both sides of the fixed frame 100. Two first drivers 210 are used to drive two groups of first pulley assemblies 220 to move up and down. The first mobile frame 230 is located in the vertical channel, and the first mobile frame 230 is slidably connected to the fixed frame 100. The first flexible cable 240 is wound above the pulley of the first pulley assembly 220, the two ends of the first flexible cable 240 extend vertically downward, one end of the first flexible cable 240 is fixed to the fixed frame 100, the other end of the first flexible cable 240 One end is fixed to the first moving fra
Embodiment 2
[0080] Figure 5 A rudder blade installation trolley is shown, which includes two rudder blade support frames 10 described in Embodiment 1, a main platform 20, a plurality of roller mechanisms 30 and two sliding mechanisms 40. A plurality of roller mechanisms 30 are located under the corners of the main platform 20 and drive the main platform 20 to move. Two sliding mechanisms 40 are slidably arranged on the main platform 20, and the two sliding mechanisms 40 are oppositely arranged and the sliding directions are parallel. Two rudder blade support frames 10 are respectively fixed on the two sliding mechanisms 40, and the two rudder blade support frames 10 are mirror images (not shown).
[0081] When using the rudder blade installation trolley to install the rudder blade, at first the rudder blade is placed between the two rudder blade support frames 10, by adjusting the distance between the two sliding mechanisms 40, the rising height of the rudder blade support frame 10, the ru
PUM
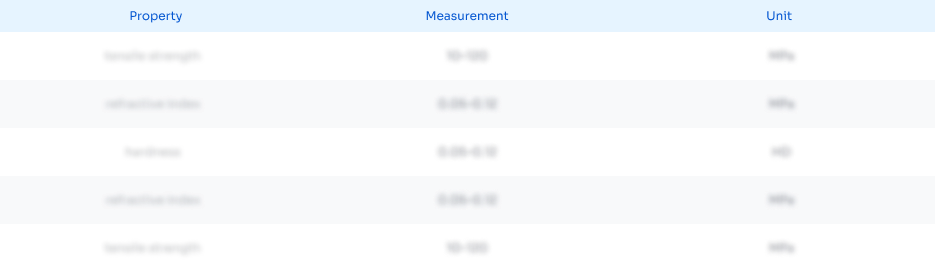
Abstract
Description
Claims
Application Information
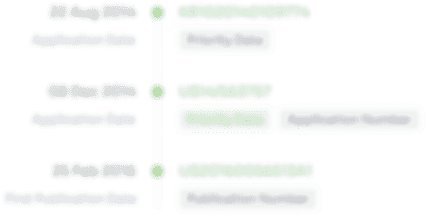
- R&D Engineer
- R&D Manager
- IP Professional
- Industry Leading Data Capabilities
- Powerful AI technology
- Patent DNA Extraction
Browse by: Latest US Patents, China's latest patents, Technical Efficacy Thesaurus, Application Domain, Technology Topic.
© 2024 PatSnap. All rights reserved.Legal|Privacy policy|Modern Slavery Act Transparency Statement|Sitemap