High-sensitivity surface acoustic wave absolute pressure sensor
A pressure sensor, surface acoustic wave technology, applied in the pressure difference measurement between multiple valves, fluid pressure measurement of elastic deformation gauge, fluid pressure measurement using acoustic method, etc., can solve the problem of complex pressure reference chamber structure, The increase in sensor volume and the difficulty in processing and preparation have achieved good long-term stability, thermal stress suppression, and good process inheritance.
- Summary
- Abstract
- Description
- Claims
- Application Information
AI Technical Summary
Benefits of technology
Problems solved by technology
Method used
Image
Examples
Embodiment
[0041] The pressure-sensitive diaphragm is made of AT-X quartz (Eulerian angle (0°, 54.7°, 0°)) piezoelectric sheet. The surface acoustic wave resonator adopts a single-ended pair resonator structure, which is made of metal Al electrodes, and the output leads are connected to the bus bars. The surface acoustic wave resonator is arranged on the inner surface of the pressure-sensitive diaphragm, at the center of the pressure-sensitive area of the pressure reference cavity, and the size of the surface acoustic wave resonator is 3mm×2mm.
[0042] The intermediate layer is made of insulating material, and the thermal expansion coefficient is similar to that of the pressure-sensitive diaphragm. The cover plate is made of AT-X quartz piezoelectric sheet, and the thermal expansion coefficient is the same as that of the pressure-sensitive diaphragm. The vacuum pressure reference cavity is realized by direct bonding.
[0043] Traditionally, square or circular pressure reference chamber
PUM
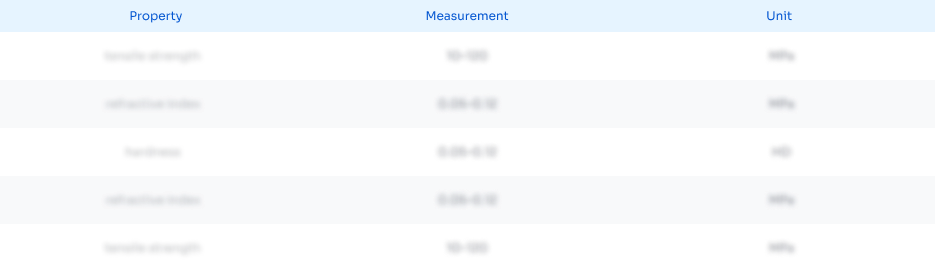
Abstract
Description
Claims
Application Information
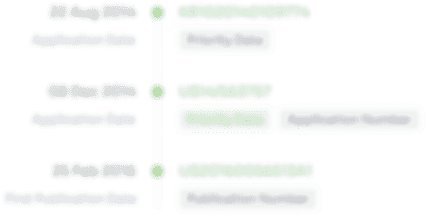
- R&D Engineer
- R&D Manager
- IP Professional
- Industry Leading Data Capabilities
- Powerful AI technology
- Patent DNA Extraction
Browse by: Latest US Patents, China's latest patents, Technical Efficacy Thesaurus, Application Domain, Technology Topic.
© 2024 PatSnap. All rights reserved.Legal|Privacy policy|Modern Slavery Act Transparency Statement|Sitemap