Preparation method of low-temperature-sensitive high-temperature-resistant polyether polyol
A polyether polyol, high temperature resistant technology, applied in the field of preparation of polyether polyol, can solve the problems of foam cracking, foam dehydration and carbonization, fracture of cross-linked structure, etc., and achieve excellent thermal stability, guaranteed strength and flow. Sex, the effect of maintaining hyposensitivity
- Summary
- Abstract
- Description
- Claims
- Application Information
AI Technical Summary
Problems solved by technology
Method used
Examples
Example Embodiment
[0023] Example 1
[0024] Put 330g of xylitol aqueous solution, 95g of trimethylolpropane, and 5g of solid KOH into the reactor, carry out the operation of sealing the reactor and raise the temperature to 100°C, and carry out the vacuum dehydration operation to control the moisture content of the material in the reactor to less than 0.1%. Control the temperature in the polymerization kettle at 102±2°C, and continuously add propylene oxide dropwise. During the process, control the actual temperature of the material to react between 102±2°C. All the propylene oxide was added dropwise and matured for 3h. Control the temperature in the kettle to be between 122±2°C, vacuumize and control the pressure in the kettle to be between -0.08 to -0.09MPa, and remove unreacted propylene oxide monomer for 1 hour. Lower the temperature in the reactor to 80±5°C, add 11.75g of phosphoric acid and 85g of water, stir for 1 hour, add 2.62g of magnesium silicate, raise the temperature to 105±5°C, an
Example Embodiment
[0025] Example 2
[0026] Put 250g of sucrose, 100g of glycerin, and 4.5g of solid KOH into the reactor, carry out the operation of sealing the reactor and raise the temperature to 100°C, and carry out the vacuum dehydration operation to control the moisture content of the material in the reactor to less than 0.1%. Control the temperature in the polymerization kettle at 102±2°C, and continuously add propylene oxide dropwise. During the process, control the actual temperature of the material to react between 102±2°C. All the propylene oxide was added dropwise and matured for 3h. Control the temperature in the kettle to be between 112±2°C, vacuumize and control the pressure in the kettle to be between -0.08 to -0.09MPa, and remove unreacted propylene oxide monomer for 1 hour. Reduce the temperature in the reactor to 80±5°C, add 10.57g of phosphoric acid and 75g of water, stir for 1 hour, add 2.25g of magnesium silicate, raise the temperature to 105±5°C, and control the pressure in
Example Embodiment
[0027] Example 3
[0028] Put 428.57g of sorbitol aqueous solution, 120g of propylene glycol, and 6.5g of solid KOH into the reactor, carry out the operation of sealing the reactor and raise the temperature to 100°C, and carry out the vacuum dehydration operation to control the moisture content of the material in the reactor to less than 0.1%. Control the temperature in the polymerization kettle at 102±2°C, and continuously add propylene oxide dropwise. During the process, control the actual temperature of the material to react between 102±2°C. All the propylene oxide was added dropwise and matured for 3h. Control the temperature in the kettle to be between 112±2°C, vacuumize and control the pressure in the kettle to be between -0.08 to -0.09MPa, and remove unreacted propylene oxide monomer for 1 hour. Reduce the temperature in the reactor to 80±5°C, add 15.27g of phosphoric acid and 104.57g of water, stir for 1 hour, add 3.14g of magnesium silicate, raise the temperature to 105
PUM
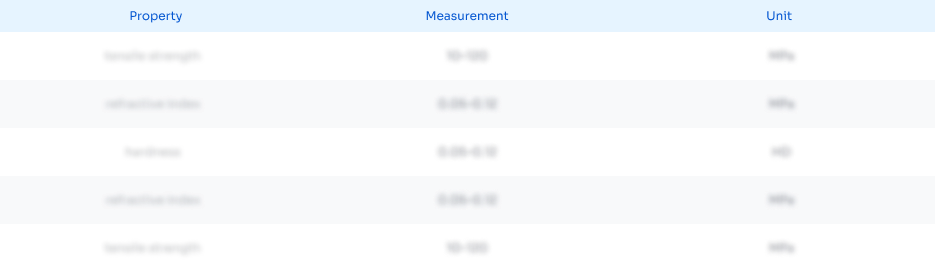
Abstract
Description
Claims
Application Information
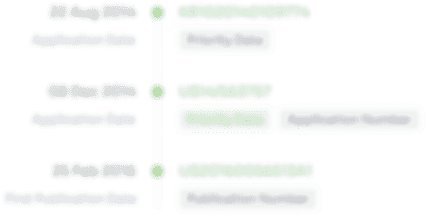
- R&D Engineer
- R&D Manager
- IP Professional
- Industry Leading Data Capabilities
- Powerful AI technology
- Patent DNA Extraction
Browse by: Latest US Patents, China's latest patents, Technical Efficacy Thesaurus, Application Domain, Technology Topic.
© 2024 PatSnap. All rights reserved.Legal|Privacy policy|Modern Slavery Act Transparency Statement|Sitemap