Surface-strengthened inner step shaft inner hole precision forming process
A surface strengthening and precision forming technology, applied in the field of machining, can solve the problems of damaged mandrel forming, long cycle, low efficiency, poor straightness, etc., and achieve the effect of applying surface compressive stress, improving fatigue resistance and improving straightness.
- Summary
- Abstract
- Description
- Claims
- Application Information
AI Technical Summary
Benefits of technology
Problems solved by technology
Method used
Image
Examples
Embodiment 1
[0044] Embodiment 1, using the integral mandrel 2-1, a surface-strengthened internal step shaft inner hole precision forming process, including the following steps:
[0045] 1) Design blank: refer to image 3 , the design length of blank 1 is L, the design inner and outer diameters are R1 and R2 respectively, the length of the raised part of the blank is W, and the height of the raised part is h2; Step length L1; billet 1 design reference ratio W:L1:(h2-h1)=(6~7):(9~10):1, the more refined billet 1 size design needs to be based on finite element simulation and experimental experience results Pick;
[0046] 2) Remove the lubricant plug 3 of the integral mandrel 2-1, pump lubricant into the lubricant main channel 4 of the integral mandrel 2-1, so that the pumped lubricant fills the lubricant main channel 4, lubricant In the inner area formed by the shunt channel 5, after the pumping is completed, the lubricant plug 3 is installed to prevent the lubricant from leaking;
[0047]3)
Embodiment 2
[0051] Embodiment 2, using the split mandrel 2-2, a surface-strengthened internal step shaft inner hole precision forming process, including the following steps:
[0052] 1) Design blank: refer to Figure 6 , the design length of blank 1 is L, the design inner and outer diameters are R1 and R2 respectively, the length of the raised part of the blank is W, and the height of the raised part is h2; -2 step length L1; billet 1 design reference ratio W:L1:(h2-h1)=(6~7):(9~10):1, the more refined billet 1 size design needs to be based on finite element simulation and experimental experience results to fetch;
[0053] 2) Remove the lubricant plug 3 of the split mandrel 2-2, pump lubricant into the main lubricant channel 4 of the split mandrel 2-2, and make the pumped lubricant fill the main lubricant channel 4, The internal area formed by the lubricant flow channel 5, after the pumping is completed, the lubricant plug 3 is installed to prevent the lubricant from leaking;
[0054] 3)
PUM
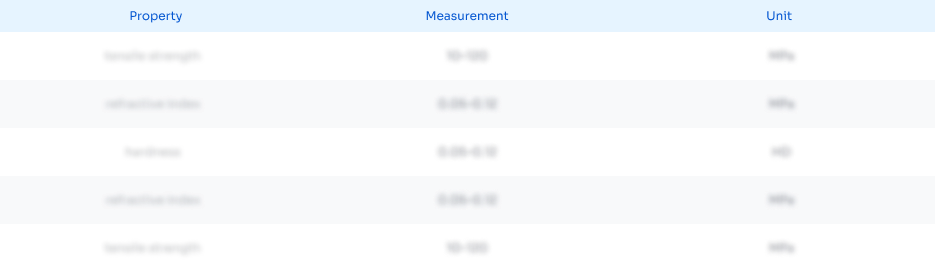
Abstract
Description
Claims
Application Information
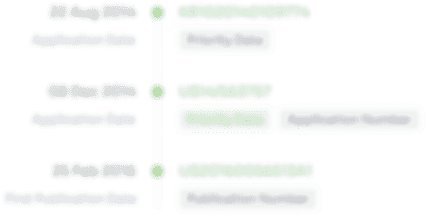
- R&D Engineer
- R&D Manager
- IP Professional
- Industry Leading Data Capabilities
- Powerful AI technology
- Patent DNA Extraction
Browse by: Latest US Patents, China's latest patents, Technical Efficacy Thesaurus, Application Domain, Technology Topic.
© 2024 PatSnap. All rights reserved.Legal|Privacy policy|Modern Slavery Act Transparency Statement|Sitemap