Reciprocating type mashing device for production of superfine calcium carbonate powder raw materials and implementation method of reciprocating type mashing device
An ultra-fine calcium carbonate, reciprocating technology, applied in the direction of liquid cleaning method, separation method, dry gas arrangement, etc., can solve environmental hazards, unsatisfactory calcium carbonate powder quality, reduce calcium carbonate production efficiency and other problems, to achieve Effects that facilitate centralized collection
- Summary
- Abstract
- Description
- Claims
- Application Information
AI Technical Summary
Problems solved by technology
Method used
Image
Examples
Example Embodiment
[0036] Example 1
[0037] A reciprocating mashing device for ultrafine calcium carbonate powder, including workbox 1, feed tube 101, cleaning tank 11, feed box 31;
[0038] The tube 101 is provided on the left side of the working case 1, and the upper end is provided with a cleaning assembly. The working box 1 is connected to the waste recovery device. The internal connection of the cleaning box 11 and the feed box 31 are connected, and the working case 1 is connected There is a universal wheel 102 with brakes, and the front end of the working case 1 is mounted with a transparent viewing window 103; the feed tube 101 passes through the working case 1, and rents into the cleaning box 11, and the cleaning box 11 is mounted with a stirring assembly, cleaning The box 11 is connected inside the bottom of the tube 11, and the cleaning box 11 bottom tube corresponds to the right side of the filter 13, the discharge port 111 is provided, and the cleaning tank 11 is connected to a connecting
PUM
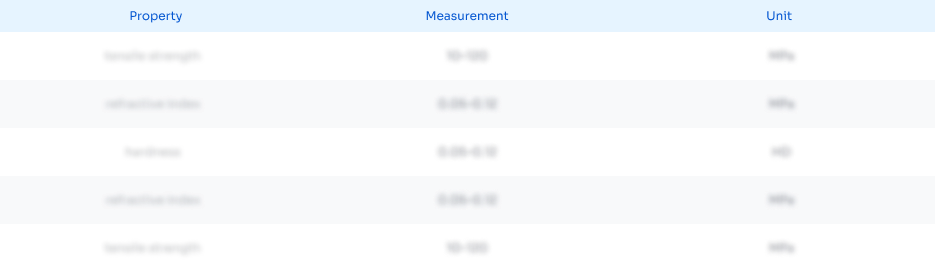
Abstract
Description
Claims
Application Information
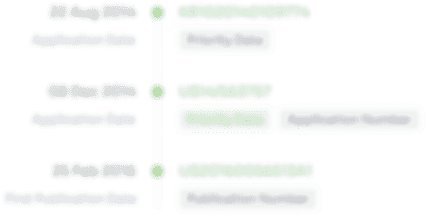
- R&D Engineer
- R&D Manager
- IP Professional
- Industry Leading Data Capabilities
- Powerful AI technology
- Patent DNA Extraction
Browse by: Latest US Patents, China's latest patents, Technical Efficacy Thesaurus, Application Domain, Technology Topic.
© 2024 PatSnap. All rights reserved.Legal|Privacy policy|Modern Slavery Act Transparency Statement|Sitemap