Analysis method for obtaining transmission stress of harmonic gear
An analysis method and technology of harmonic gears, applied in special data processing applications, instruments, geometric CAD, etc., can solve the problems of inconsistent stress distribution in analysis results, unclear application of boundary conditions, and inaccurate strength analysis results. Accurate and efficient strength analysis results, extracting the stress distribution of harmonic gear transmission, and the effect of standardized analysis steps
- Summary
- Abstract
- Description
- Claims
- Application Information
AI Technical Summary
Benefits of technology
Problems solved by technology
Method used
Image
Examples
Embodiment Construction
[0029] The following is further described in detail through specific implementation methods:
[0030] Such as figure 2 The shown harmonic gear reducer includes a wave generator (composed of cam 4 and flexible bearing 3), flexible spline 1 and rigid spline 2, the flexible spline 1 and rigid spline 2 are meshed, the wave generator is in contact with the inner wall of the flexible spline 1, and the cam 4 Wearing in the inner ring of the flexible bearing 3, the outer ring of the flexible bearing 3 is in contact with the inner wall of the flexspline 1, and the finite element modeling analysis method for obtaining the stress of the harmonic gear transmission includes the following figure 1 The following steps are shown:
[0031] S1: According to the structure of the harmonic gear reducer, use the 3D modeling software SolidWorks to establish the assembly model of the harmonic gear reducer including the wave generator, flexible spline, and rigid spline, and export the step format file
PUM
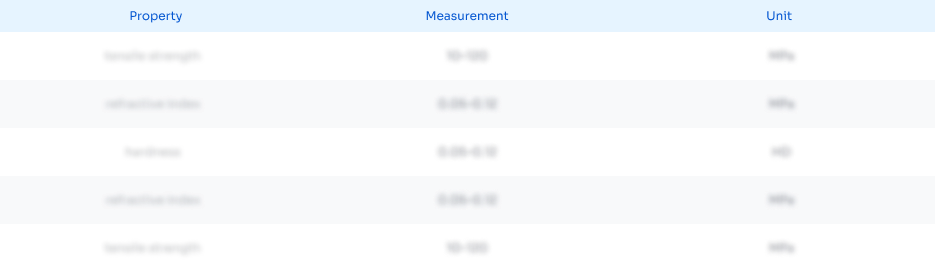
Abstract
Description
Claims
Application Information
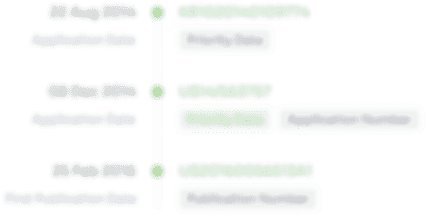
- R&D Engineer
- R&D Manager
- IP Professional
- Industry Leading Data Capabilities
- Powerful AI technology
- Patent DNA Extraction
Browse by: Latest US Patents, China's latest patents, Technical Efficacy Thesaurus, Application Domain, Technology Topic.
© 2024 PatSnap. All rights reserved.Legal|Privacy policy|Modern Slavery Act Transparency Statement|Sitemap