Method for producing black iron oxide by liquid phase synthesis
A kind of iron oxide black, uniform technology, applied in the field of liquid phase additive production of iron oxide black, can solve the problems of production cost reduction, environmental pollution, volatilization, etc., achieve the effects of efficient utilization, quality improvement, and chemical stability improvement
- Summary
- Abstract
- Description
- Claims
- Application Information
AI Technical Summary
Problems solved by technology
Method used
Examples
Embodiment 1
[0020] Add 0.5% ferrous sulfate solution preheated to 70°C into the reaction kettle, keep it warm at 70-95°C, and let air flow in at 25M 3 Under the condition of / min, add NaOH solution, ferrous sulfate and sodium hydroxide take place addition reaction, generate iron ferric oxide, after reaction is finished, stop stirring, ferric oxide sedimentation gathers at the bottom of the reactor, after the sedimentation is completed Remove the supernatant, keep the generated ferric oxide in the reaction kettle, continue to add 0.5% ferrous sulfate solution preheated to 70°C into the reaction kettle, add NaOH solution, and pass in air 25M 3 / min, continue to generate ferric oxide at 70-95°C. In this way, in a reaction kettle, the reaction produces ferric oxide - ferric oxide settles - removes the supernatant and circulates 3 times, collects and washes the precipitate, and then undergoes conventional pressure filtration, drying, and grinding to obtain iron oxide black.
Embodiment 2
[0022] Add 0.5% ferrous sulfate solution preheated to 70°C into the reaction kettle, keep it warm at 80-95°C, and let air flow in at 30M 3 Under the condition of / min, add NaOH solution, ferrous sulfate and sodium hydroxide take place addition reaction, generate iron ferric oxide, after reaction is finished, stop stirring, ferric oxide sedimentation gathers at the bottom of the reactor, after the sedimentation is completed Remove the supernatant, keep the generated ferric oxide in the reactor, continue to add 0.5% ferrous sulfate solution preheated to 70°C into the reactor, add NaOH solution, and feed the air at a rate of 30M 3 / min, continue to generate ferric oxide at 70-95°C. In this way, in a reaction kettle, the reaction produces ferric oxide - ferric oxide settles - removes the supernatant and circulates 5 times, collects and washes the precipitate, and then undergoes conventional pressure filtration, drying, and grinding to obtain iron oxide black.
Embodiment 3
[0024] Add 0.5% ferrous sulfate solution preheated to 70°C into the reaction kettle, keep it warm at 80-95°C, and let air flow in at 30M 3 Under the condition of / min, add NaOH solution, ferrous sulfate and sodium hydroxide take place addition reaction, generate iron ferric oxide, after reaction is finished, stop stirring, ferric oxide sedimentation gathers at the bottom of the reactor, after the sedimentation is completed Remove the supernatant, keep the generated ferric oxide in the reactor, continue to add 0.5% ferrous sulfate solution preheated to 70°C into the reactor, add NaOH solution, and feed the air at a rate of 30M 3 / min, continue to generate ferric oxide at 70-95°C. In this way, in a reaction kettle, the reaction produces ferric oxide - ferric oxide settles - removes the supernatant and circulates 8 times, collects and washes the precipitate, and then undergoes conventional pressure filtration, drying, and grinding to obtain iron oxide black.
PUM
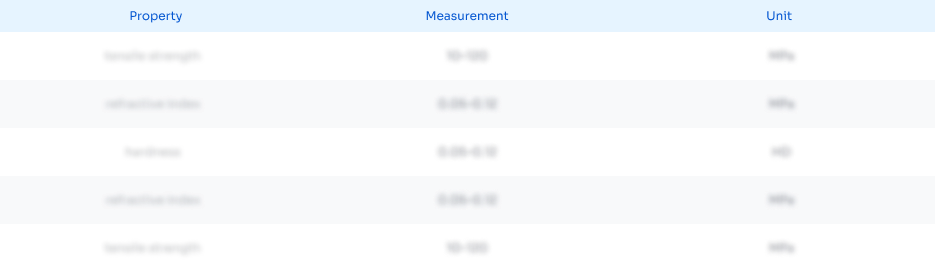
Abstract
Description
Claims
Application Information
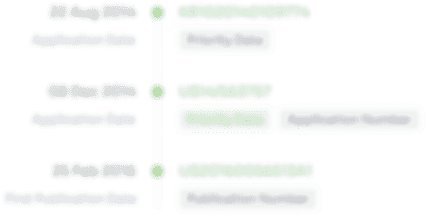
- R&D Engineer
- R&D Manager
- IP Professional
- Industry Leading Data Capabilities
- Powerful AI technology
- Patent DNA Extraction
Browse by: Latest US Patents, China's latest patents, Technical Efficacy Thesaurus, Application Domain, Technology Topic.
© 2024 PatSnap. All rights reserved.Legal|Privacy policy|Modern Slavery Act Transparency Statement|Sitemap