Steel mold for prefabricated concrete lintel of distribution box, and assembly structure and construction method of steel mold
A technology for concrete and distribution boxes, which is applied in the direction of manufacturing tools, mold fixtures, molds, etc., can solve problems such as damage to masonry, and achieve the effects of ensuring construction quality, good appearance, and improving production efficiency
- Summary
- Abstract
- Description
- Claims
- Application Information
AI Technical Summary
Problems solved by technology
Method used
Examples
Example Embodiment
[0037] Example 1:
[0038] See Figures 1 to 11 According to a prefabricated distribution tab of concrete, a beam steel mold comprising a bottom mold 1, a short side mold 2, a long side surface 3, a top mold 4, a die 5, and a bolt 6, the bottom mold 1, short The side mold 2, the long side mold 3 and the top mold 4 are all made of but not limited to metal sheets, and steel sheets are used in general. The bottom mold 1 is in a rectangle, and the two short sides of the upper portion thereof are opened in the inside of the two long sides, respectively, the short side groove 101 and the long side groove 102, which are parallel to the short side and the long side and the depth are respectively. There are several circular wire buckle grooves 103 in the long side corresponding center line; the short side mold 2 is a rectangular shape, and a bolt hole 202 is provided on both sides thereof, and the bottom portion is provided with a short side groove 101. The attached card block 203 is adjusted
Example Embodiment
[0042] Example 2:
[0043] Example 1 A prefabricated distribution tank concrete beam mold assembly structure, which is: two pieces of the short side surface 2 and the long side mold 3, two short side side molds 2 pass the card, respectively. The block 203 is bicked into the short side groove 102 and is fixedly coupled to the bottom mold 1, and the two sides of the two long edge sides 3 are collated into the slot 201 corresponding to the two short side side molds 2, the bottom card Inside the groove 102; the top mold 4 is lid on the short side surface 2 and the long side surface 3, and the four circular holes 403 thereon correspond to each of the bolt holes 202, respectively, and respectively through the bolt 6, respectively. The corresponding circular holes 403 and the bolt hole 202 are connected; each of the circular wire buckle grooves 103 is coupled to the outer thread 501 of the bottom of the ferrule 5, the top of the ferrule 501 from the circular wire buckle. The rounded hole 40
Example Embodiment
[0044] Example 3:
[0045] The construction method of a steel mold for a prefabricated distribution tank concrete beam is carried out using a steel mold of the prefabricated distribution tank concrete beam according to Example 1, including the following steps:
[0046] Step 1, first place the bottom mold 1 on the horizontal floor;
[0047] Step 2, the short-side side mold 2 is snap into the short side groove 101 on both sides of the bottom mold 1;
[0048] Step three, insert the long side mold 3 inserted into the slot 201 and the long side groove 102 of the bottom mold 1 on both sides of the two short side molds 1.
[0049] Step 4, place the top mold 4 at the top of the short side mold 2 and the long side mold 3, align the bolt hole 202 at the top of the two short side mold 2, and by bolts 6 Fixed tightening;
[0050] Step 5, according to the actual desired, the outer thread 501 of the core 5 of the top mold 4 is slightly fixed to the outer thread 501 corresponding to the bottom mold
PUM
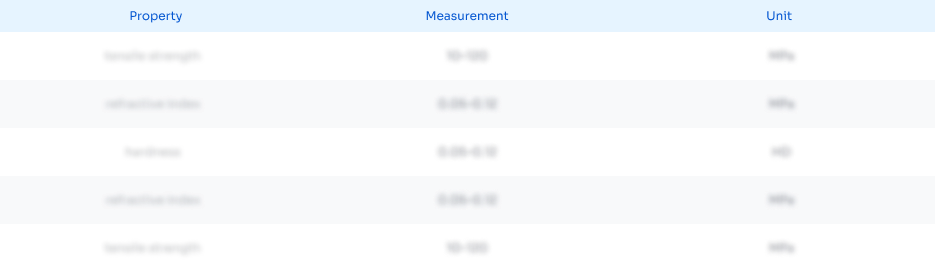
Abstract
Description
Claims
Application Information
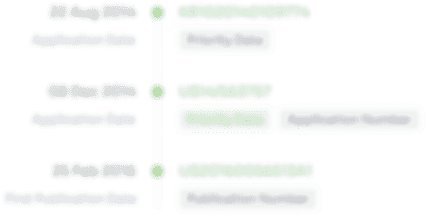
- R&D Engineer
- R&D Manager
- IP Professional
- Industry Leading Data Capabilities
- Powerful AI technology
- Patent DNA Extraction
Browse by: Latest US Patents, China's latest patents, Technical Efficacy Thesaurus, Application Domain, Technology Topic.
© 2024 PatSnap. All rights reserved.Legal|Privacy policy|Modern Slavery Act Transparency Statement|Sitemap