Efficient and automatic welding process for rack and semi-chord pipe
An automatic welding and chord technology, applied in welding equipment, welding accessories, manufacturing tools, etc., can solve the problems that restrict the delivery time of the platform, the market competitiveness of enterprises, the welding depth does not reach the thickness of the plate, and the stability of difficult welding quality. Reduce post-weld repair costs, reduce work intensity and requirements, and reduce spatter
- Summary
- Abstract
- Description
- Claims
- Application Information
AI Technical Summary
Problems solved by technology
Method used
Examples
Example Embodiment
[0031] Example:
[0032] like figure 1 , figure 2 As shown, this embodiment is applied to the welding of 70mm thick Q690 and rack steel, and the specific process is as follows:
[0033] 1) For the connection between the half chord plate and the rack plate of different thicknesses, design appropriate narrow grooves, the low end blunt edge of the groove is 0mm, the bottom diameter is 12mm, and the groove angle is 3°.
[0034] 2) Select the matching 1.2mmER110S-G solid core gas shielded welding wire.
[0035] 3) Before welding, use mechanical grinding to remove rust, oil, moisture and other impurities on the surface of the steel plate to ensure the welding quality.
[0036] 4) Carry out welding group pairing and spot welding to fix.
[0037] 5) After the groove is paired, it is necessary to connect the arc strike plate with the same shape as the groove at the beginning and end of the weld bead to avoid defects such as pores in the actual welding area.
[0038] 6) Select the mi
PUM
Property | Measurement | Unit |
---|---|---|
Bottom diameter | aaaaa | aaaaa |
Groove angle | aaaaa | aaaaa |
Abstract
Description
Claims
Application Information
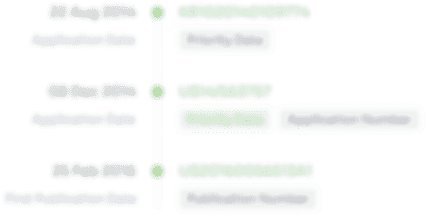
- R&D Engineer
- R&D Manager
- IP Professional
- Industry Leading Data Capabilities
- Powerful AI technology
- Patent DNA Extraction
Browse by: Latest US Patents, China's latest patents, Technical Efficacy Thesaurus, Application Domain, Technology Topic.
© 2024 PatSnap. All rights reserved.Legal|Privacy policy|Modern Slavery Act Transparency Statement|Sitemap