Method for making artificial fiber pulp by whole hemp stalk
A man-made fiber and pulp technology, applied in fiber raw material processing, pulp bleaching, textile and papermaking, etc., can solve problems such as affecting cooking quality, inconsistent and changing liquid penetration effect, etc.
- Summary
- Abstract
- Description
- Claims
- Application Information
AI Technical Summary
Problems solved by technology
Method used
Examples
Embodiment 1
[0027] 1. Cutting: cutting length of hemp stalk: 20mm;
[0028] 2. Grinding and splitting: speed: 500r / min; natural bulk density: 150g / L;
[0029] 3. Cooking: charging volume: 140kg / m 3 ; Liquid ratio: 1:3.0; NaOH dosage: 8%; holding time: 180 minutes; holding temperature: 145°C;
[0030] 4. Bleaching: chlorine amount for chlorination: 1.5%; alkali amount for alkali refining: 3%; alkali refining time: 60 minutes;
[0031] Alkali refining temperature: 60°C; bleaching chlorine: 1.2%; bleaching temperature: 40°C;
[0032] Bleaching pH value: 13; Bleaching time: 90 minutes; Adding amount of sodium hexametaphosphate: 2‰;
[0033] 5. Finished product:
[0034] Fiber: 93.6%; Moisture: 10.1%; Viscosity: 10.3mpas; Whiteness: 80%; Ash: 0.13%; Iron: 18ppm; Pentose: 1.7%; Lignin: 0.23%;
Embodiment 2
[0036] 1. Cutting: cutting length of hemp stalk: 35mm;
[0037] 2. Grinding and splitting: speed: 350r / min; natural bulk density: 130g / L;
[0038] 3. Cooking: charging amount: 150kg / m 3 ; Liquid ratio: 1:4.0; NaOH dosage: 10%; holding time: 165 minutes; holding temperature: 155°C;
[0039] 4. Bleaching: chlorine amount for chlorination: 2.0%; alkali amount for alkali refining: 2%; alkali refining time: 75 minutes;
[0040] Alkali refining temperature: 70°C; bleaching chlorine: 0.8%; bleaching temperature: 42°C;
[0041] Bleaching pH value: 12; Bleaching time: 105 minutes; Adding amount of sodium hexametaphosphate: 2.5‰;
[0042] 5. Finished product:
[0043] A fiber: 93.8%; Moisture: 11.2%; Viscosity: 10.8mpas; Whiteness: 81%; Ash: 0.12%; Iron: 20ppm; Pentose: 1.9%; Lignin: 0.20%;
Embodiment 3
[0045] 1. Cutting: cutting length of hemp stalk: 50mm;
[0046] 2. Grinding and splitting: speed: 260r / min; natural bulk density: 120g / L
[0047] 3. Cooking: charging volume: 160kg / m 3 ; Liquid ratio: 1:4.5; NaOH dosage: 12%; holding time: 150 minutes; holding temperature: 165°C;
[0048] 4. Bleaching: chlorine amount for chlorination: 2.5%; alkali amount for alkali refining: 1%; alkali refining time: 90 minutes;
[0049] Alkali refining temperature: 60°C; bleaching chlorine: 0.5%; bleaching temperature: 45°C;
[0050] Bleaching pH value: 11; Bleaching time: 120 minutes; Adding amount of sodium hexametaphosphate: 3‰;
[0051] 5. Finished product:
[0052] A fiber: 93.5%; moisture: 9.8%; viscosity: 10.6mpas; whiteness: 80%; ash: 0.11%; iron: 17ppm; pentose: 2.2%; lignin: 0.15%; .
PUM
Property | Measurement | Unit |
---|---|---|
Viscosity | aaaaa | aaaaa |
Viscosity | aaaaa | aaaaa |
Viscosity | aaaaa | aaaaa |
Abstract
Description
Claims
Application Information
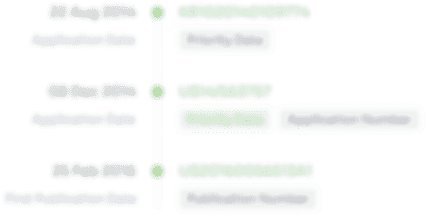
- R&D Engineer
- R&D Manager
- IP Professional
- Industry Leading Data Capabilities
- Powerful AI technology
- Patent DNA Extraction
Browse by: Latest US Patents, China's latest patents, Technical Efficacy Thesaurus, Application Domain, Technology Topic.
© 2024 PatSnap. All rights reserved.Legal|Privacy policy|Modern Slavery Act Transparency Statement|Sitemap