Preparation method of hydrogenated process catalyst
A hydrogenation treatment and catalyst technology, which is applied in the treatment of hydrocarbon oil and petroleum industry, etc., can solve the problems of reduced pore volume and specific surface area, low hydrogenation activity, and reduced reaction contact area, so as to improve pore volume and specific surface area, Effect of improving usability and latent activity
- Summary
- Abstract
- Description
- Claims
- Application Information
AI Technical Summary
Benefits of technology
Problems solved by technology
Method used
Examples
preparation example Construction
[0009] The preparation method of the catalyst of the present invention is that the powdery bulk catalyst prepared by the co-precipitation method is fully contacted with the ammonium salt compound of fluorine, the fluorine ion is combined with the bulk catalyst, and the released ammonia is absorbed by the micropores of the bulk catalyst; then the bulk catalyst powder is After adding an acidic solution or an acidic binder, it is molded, dried and calcined to make a catalyst. Specifically, the present invention may include the following steps:
[0010] (1) metal compound solution co-precipitation;
[0011] (2) removing all or part of the water and pulverizing the precipitate obtained in step (1) to make bulk catalyst powder;
[0012] (3) the bulk catalyst powder that step (2) obtains is fully contacted with the ammonium salt compound of fluorine;
[0013] (4) forming after mixing the bulk catalyst powder of adsorbing ammonia or ammonium obtained in step (3) with an acidic solution
Embodiment 1
[0028] Prepare bulk catalyst powder by the method described in CN1342102A.
[0029] (1) Dissolve and mix ammonium heptamolybdate and ammonium metatungstate fully in the first reactor, and raise the temperature to 90°C.
[0030] (2) Aqueous ammonia is added to the first reactor to form an alkaline solution.
[0031] (3) Dissolve nickel nitrate in the second reactor and heat to 90°C.
[0032] (4) Add the solution obtained in step (3) dropwise into the first reactor under stirring, stir the formed suspension for another 30 minutes, filter and wash the precipitate, and place the precipitate in air at 120°C Dry for 5 hours, heat-treat at 385° C. in air for 1 hour, then pulverize and sieve with a 180-mesh sieve to obtain bulk catalyst powder.
[0033] In the above process, various materials are charged according to the bulk catalyst and contain 38.9w% NiO, 22.2w% MoO 3 and 38.9w% WO 3 The proportion of feeding.
Embodiment 2
[0035] The method of the invention prepares the catalyst.
[0036] (1) 0.06mol nitric acid, 120ml water and 15g (dry basis) SB-alumina powder (produced in Germany) were fully mixed and peptized to make a binder.
[0037] (2) Add 8g of ammonium fluoride and 85g (dry basis) powder of the bulk catalyst prepared in Example 1 into an airtight mixer for sufficient contact and mixing.
[0038] (3) After uniformly mixing the ammonia-adsorbed bulk catalyst powder obtained in step 2 with the binder obtained in step 1, extrude to make a catalyst precursor.
[0039] (4) Dry the catalyst precursor obtained in step 3 at 120° C. in air for 2 hours.
[0040] (5) Treat the catalyst dry strip obtained in step 4 under the catalyst at 350° C. for 1 hour. The prepared catalyst is denoted as catA.
PUM
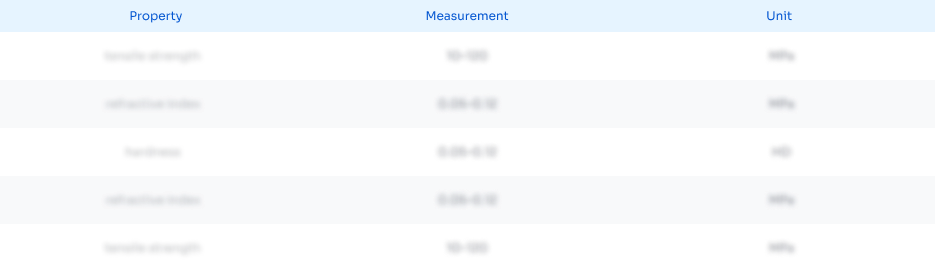
Abstract
Description
Claims
Application Information
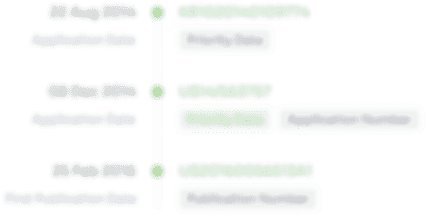
- R&D Engineer
- R&D Manager
- IP Professional
- Industry Leading Data Capabilities
- Powerful AI technology
- Patent DNA Extraction
Browse by: Latest US Patents, China's latest patents, Technical Efficacy Thesaurus, Application Domain, Technology Topic.
© 2024 PatSnap. All rights reserved.Legal|Privacy policy|Modern Slavery Act Transparency Statement|Sitemap