Emulsion type fluorine-containing textile finishing agent and preparation method thereof
A technology for fluorine-containing fabrics and finishing agents, which is used in water-repellent finishing. , In the field of oil repellency, it can solve the problem that the durability of the finishing agent needs to be further improved, and achieve the effect of good application prospect, excellent water repellency and strong adhesion ability.
- Summary
- Abstract
- Description
- Claims
- Application Information
AI Technical Summary
Problems solved by technology
Method used
Examples
Example Embodiment
[0034] Example 1
[0035] According to the following proportions, take 35.00g of monomers perfluoroalkyl ethyl acrylate, 9.60g of methyl methacrylate, 8.60g of stearyl acrylate, 3.60g of methylol acrylamide, and cyanoacetoxyethyl methacrylic acid Ester 0.80g, chain transfer agent lauryl mercaptan 0.12g, emulsifier sodium lauryl sulfate 1.58g, fatty alcohol polyoxyethylene ether OS-151.60g, deionized water 118.40ml in the reaction vessel after high pressure homogenization Emulsify with a mass machine to obtain a stable pre-emulsion. Take 0.7g of 2,2'-azobis(2-amidinopropane) dihydrochloride and dissolve it in 20ml of deionized water. Add 1 / 5 of the pre-emulsion to a stirred Into the reactor of the reactor, thermometer and condenser, after nitrogen deoxygenation, stir and heat, increase the temperature to 50~80℃, add 1 / 5 initiator, and after reacting for half an hour, add the remaining pre-emulsion and initiator dropwise. After 3 hours of dripping, the reaction is continued for 6 h
Example Embodiment
[0037] Example 2
[0038]According to the following proportions, take 42.00g of monomer perfluoroalkyl ethyl acrylate, 6.40g of lauryl acrylate, 9.40g of acrylonitrile, 3.80g of hydroxyethyl acrylate, and 1.68g of ureidoethyl methacrylate QM-1558. Transfer agent dodecyl mercaptan 0.12g, emulsifier octadecyl trimethyl ammonium chloride 2.00g, fatty alcohol polyoxyethylene ether O-9 1.60g, deionized water 111.20ml, ultrasonic wave in the reaction vessel The emulsifier emulsifies to obtain a stable pre-emulsion. Take 1.8 g of 2,2'-azobis(2-amidinopropane) dihydrochloride and dissolve it in 20ml of deionized water. Add 1 / 5 of the pre-emulsion to a stirred Into the reactor of the reactor, thermometer and condenser, after nitrogen deoxygenation, stir and heat, increase the temperature by 50~80℃, add 1 / 5 initiator, and after reacting for half an hour, add the remaining pre-emulsion and initiator respectively. After 3 hours, the dripping is completed and the reaction is continued for 6 h
Example Embodiment
[0040] Example 3
[0041] According to the ratio of the following table, take the monomers 47.60g of perfluoroalkyl ethyl acrylate, 5.00g of methyl acrylate, 5.80g of stearyl methacrylate, 1.20g of methacrylic acid, 2.40g of methylol acrylamide, and allyl Urea ethyl ether WAM II 1.80g, chain transfer agent lauryl mercaptan 0.18g, emulsifier sodium lauryl sulfonate 2.40g, nonylphenol polyoxyethylene ether OP-10 3.60g, deionized water 108.8ml, emulsify in a reaction vessel with a high-pressure homogenizer to obtain a stable pre-emulsion, take 1.22 g of 2,2'-azobisisobutamidine dihydrochloride and dissolve it in 20ml of deionized water, and add the pre-emulsion 1 / 5 was added to a reactor equipped with a stirrer, thermometer and condenser. After nitrogen was introduced to deoxygenate, it was stirred and heated, and the temperature was raised to 50~80℃. 1 / 5 of the initiator was added. After half an hour of reaction, the remaining was added dropwise. Pre-emulsion liquid and initiator,
PUM
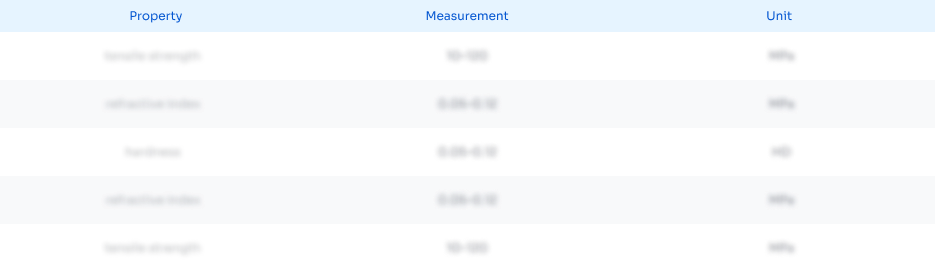
Abstract
Description
Claims
Application Information
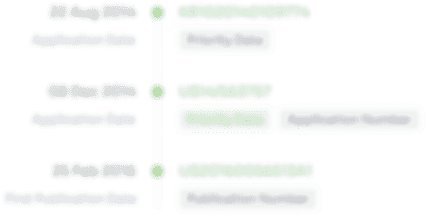
- R&D Engineer
- R&D Manager
- IP Professional
- Industry Leading Data Capabilities
- Powerful AI technology
- Patent DNA Extraction
Browse by: Latest US Patents, China's latest patents, Technical Efficacy Thesaurus, Application Domain, Technology Topic.
© 2024 PatSnap. All rights reserved.Legal|Privacy policy|Modern Slavery Act Transparency Statement|Sitemap