Methods and apparatus for assembling gas turbine engine stator assemblies
a technology for gas turbine engines and stator assemblies, which is applied in the field of gas turbine engines, can solve the problems of undetectable slippage of known spline seals, damage to other engine components, and limit the useful life of the turbine nozzle, so as to facilitate reducing leakage, facilitate retaining, and facilitate the effect of reducing leakag
- Summary
- Abstract
- Description
- Claims
- Application Information
AI Technical Summary
Benefits of technology
Problems solved by technology
Method used
Image
Examples
Embodiment Construction
[0016]FIG. 1 is a schematic illustration of an exemplary gas turbine engine 10 including a low pressure compressor 12, a high pressure compressor 14, and a combustor 16. Engine 10 also includes a high pressure turbine 18 and a low pressure turbine 20. Compressor 12 and turbine 20 are coupled by a first shaft 21, and compressor 14 and turbine 18 are coupled by a second shaft 22. In one embodiment, gas turbine engine 10 is an LM2500 engine commercially available from General Electric Aircraft Engines, Cincinnati, Ohio. In another embodiment, gas turbine engine 10 is a CFM engine commercially available from General Electric Aircraft Engines, Cincinnati, Ohio.
[0017] In operation, air flows through low pressure compressor 12 supplying compressed air from low pressure compressor 12 to high pressure compressor 14. The highly compressed air is delivered to combustor 16. Airflow from combustor 16 is channeled through a turbine nozzle (not shown in FIG. 1) to drive turbines 18 and 20, prior to
PUM
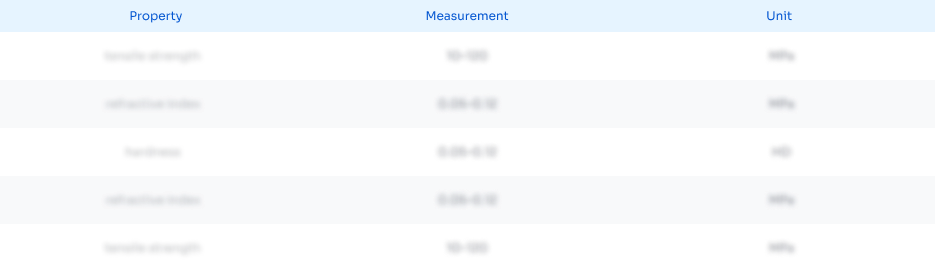
Abstract
Description
Claims
Application Information
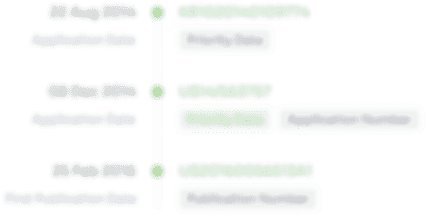
- R&D Engineer
- R&D Manager
- IP Professional
- Industry Leading Data Capabilities
- Powerful AI technology
- Patent DNA Extraction
Browse by: Latest US Patents, China's latest patents, Technical Efficacy Thesaurus, Application Domain, Technology Topic.
© 2024 PatSnap. All rights reserved.Legal|Privacy policy|Modern Slavery Act Transparency Statement|Sitemap