Electric discharge machine and electric discharge machining method
a technology of electric discharge machine and machining method, which is applied in water/sewage treatment, water/sludge/sewage treatment, chemistry apparatus and processes, etc., can solve problems such as deterioration of workpiece quality, and achieve the effect of preventing corrosion of workpieces
- Summary
- Abstract
- Description
- Claims
- Application Information
AI Technical Summary
Benefits of technology
Problems solved by technology
Method used
Image
Examples
first embodiment
[0023]FIG. 1 is a block diagram showing an electrical wire discharge machine according to a first embodiment of the present invention. The electrical wire discharge machine proceeds with machining by applying a voltage between a workpiece 1 and a wire electrode 2 within a working tank 8; and causing an electrical discharge through a dielectric fluid squirted from an upper dielectric fluid nozzle 4 and a dielectric fluid squirted from a lower dielectric fluid nozzle 5, to thus fuse and eliminate the target areas of the workpiece 1.
[0024]At this time, an electrical discharge portion of the wire electrode 2 is also fused / deteriorated in accordance with a progress in electrical discharge operation. Accordingly, the wire electrode 2 wound around a wire bobbin 3 is continuously fed to a recovery box 7 through the upper dielectric fluid nozzle 4, the lower dielectric fluid nozzle 5, and a recovery roller 6 so that a new wire electrode 2 is fed to the machining section in association with a
second embodiment
[0061]In the present embodiment, the working tank 8 is imparted with the function of the anticorrosive electrode as shown in FIG. 5.
[0062]According to the configuration, the working tank 8 and the table 9 are insulated from each other by the mount 10. The dielectric fluid exists between the working tank 8 and the table 9. Hence, the insulator 24 becomes obviated. Further, the area of the electrode is wide, and hence the electrical resistance of the electrode is lowered, which in turn enables a reduction in voltage and current.
[0063]By the wire electrical discharge machine having the method for preventing corrosion of a workpiece, which would otherwise be caused by application of the voltage, the conductivity of the dielectric fluid was controlled to 6.2 μS / cm (corresponding to a pH value of 9.0). Further, a voltage of 3 volts was applied between the table 9 and the working tank 8. Thus, corrosion of a superhard material (WC-Co) or an iron-based material (SKD-11) was prevented during
PUM
Property | Measurement | Unit |
---|---|---|
Electric potential / voltage | aaaaa | aaaaa |
Electrical conductivity | aaaaa | aaaaa |
Electric potential / voltage | aaaaa | aaaaa |
Abstract
Description
Claims
Application Information
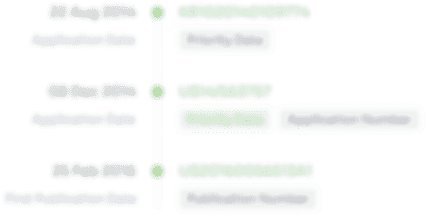
- R&D Engineer
- R&D Manager
- IP Professional
- Industry Leading Data Capabilities
- Powerful AI technology
- Patent DNA Extraction
Browse by: Latest US Patents, China's latest patents, Technical Efficacy Thesaurus, Application Domain, Technology Topic.
© 2024 PatSnap. All rights reserved.Legal|Privacy policy|Modern Slavery Act Transparency Statement|Sitemap