Automated warehouse system
a warehouse system and stacker crane technology, applied in the field of automatic warehouse systems, can solve the problems of limiting the ability to reduce requiring a large amount of space, and reducing the space in the warehous
- Summary
- Abstract
- Description
- Claims
- Application Information
AI Technical Summary
Benefits of technology
Problems solved by technology
Method used
Examples
first embodiment
[0033]A first embodiment will be explained below based on the appended drawings. An overall perspective diagram of an automated warehouse system 20 according to the first embodiment is illustrated in FIG. 1. To facilitate viewing of the movable platform 50, the drawing omits a portion of one of the storage shelves 100.
[0034]Structure of the Automated Warehouse System 20
[0035]As illustrated in FIG. 1, the automated warehouse system 20 according to the first embodiment has a pair of storage shelves 100 having a plurality of storage areas RC. The storage shelves 100 have storage areas RC wherein loads BG are stored, and storage areas RC wherein loads BG are not yet stored. The movable platform 50 transfers a load BG from a loading / unloading port 101 (shown in FIG. 2 (A)) to a specific storage area RC, or transfers a load BG that is stored in a storage area RC to the loading / unloading port 101, following a movement instruction from a controlling portion MA.
[0036]FIG. 2 (A) is a side vie...
second embodiment
[0085]An automated warehouse system 22 according to a second embodiment has a plurality of storage shelves 100 (100A through 100D). FIG. 9 is a side view diagram, viewed from the X direction, of the automated warehouse system 22.
[0086]The automated warehouse system 22 according to the second embodiment has four storage shelves 100 (100A through 100D), each having a plurality of storage areas RC. A plurality of movable platforms 50 is disposed between the storage shelves 100A and 100B. Similarly, a plurality of movable platforms 50 is disposed between the storage shelves 100B and 100C, and a plurality of movable platforms 50 is disposed between the storage shelves 100C and 100D. The Y-direction width WY1 of the storage shelves 100 and the Y-direction width WY2 of the movable platforms 50 are essentially identical.
[0087]The storage shelf 100B and the storage shelf 100C each have a plurality of movable platforms 50 disposed on both sides of each. Moreover, as illustrated in FIG. 4 or F...
third embodiment
[0089]An automated warehouse system 24 according to a third embodiment has a plurality of storage shelves 100 (100A through 100D). FIG. 10 is a side view diagram, viewed from the X direction, of the automated warehouse system 24.
[0090]The automated warehouse system 24 according to the third embodiment has four storage shelves 100 (100A through 100D), each having a plurality of storage areas RC. A plurality of movable platforms 50 is disposed between the storage shelves 100A and 100B. The storage shelf 100B and the storage shelf 100C adjoin each other, with no room for a movable platform 50 between the storage shelf 100B and the storage shelf 100C. A plurality of movable platforms 50 is disposed between the storage shelves 100C and 100D. The Y-direction width WY1 of the storage shelves 100 and the Y-direction width WY2 of the movable platforms 50 are essentially identical.
[0091]Even though the storage shelves 100B and storage shelf 100C adjoin each other, the movable platforms 50 on ...
PUM
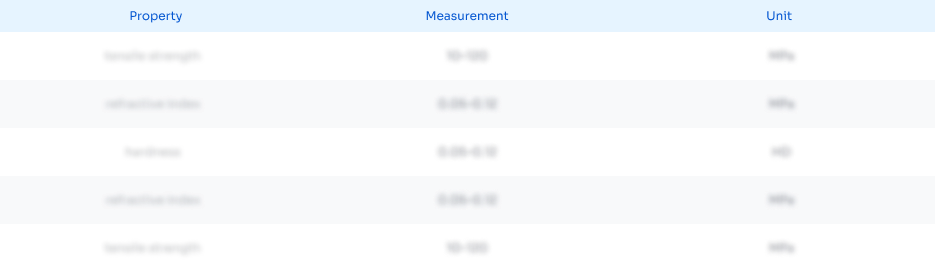
Abstract
Description
Claims
Application Information
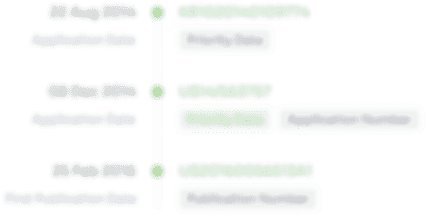
- R&D Engineer
- R&D Manager
- IP Professional
- Industry Leading Data Capabilities
- Powerful AI technology
- Patent DNA Extraction
Browse by: Latest US Patents, China's latest patents, Technical Efficacy Thesaurus, Application Domain, Technology Topic.
© 2024 PatSnap. All rights reserved.Legal|Privacy policy|Modern Slavery Act Transparency Statement|Sitemap