Electric brake system and operating method thereof
- Summary
- Abstract
- Description
- Claims
- Application Information
AI Technical Summary
Benefits of technology
Problems solved by technology
Method used
Examples
Example
[0054]Referring to FIG. 1, an electric brake system 1 according to the first embodiment may include a master cylinder 20, a reservoir 30, a wheel cylinder 40, a simulator, a hydraulic supplier 100, a hydraulic control unit 200, and an electronic control unit (ECU; not shown). The master cylinder 20 is configured to press and discharge pressure medium such as brake oil contained therein, by a pedal effort of a brake pedal 10. The reservoir 30 is configured to store the pressure medium by being communicated with the master cylinder 20. The wheel cylinder 40 is configured to brake each vehicle wheel; rear right wheel (RR), rear left wheel (RL), front right wheel (FR) and front left wheel (FL) by receiving a hydraulic pressure of the pressure medium. The simulator 50 is configured to provide a reaction force against the pedal effort of the brake pedal 10, to a driver. The hydraulic supplier 100 is configured to generate a hydraulic pressure of the pressure medium through a mechanical opera
Example
[0198]Hereinafter, an electric brake system 2 according to a second embodiment of will be described.
[0199]In the following description of the electric brake system 2 according to the second embodiment, except for an additional description with a different reference numeral, a description of the same parts as those shown in the electric brake system 1 according to the first embodiment will be omitted to prevent duplication.
[0200]FIG. 10 is a hydraulic circuit diagram illustrating an electric brake system 2 according to the second embodiment.
[0201]Referring to FIG. 10, according to the second embodiment, a first hydraulic flow path 211 of the electric brake system 2 may connect a first pressure chamber 112 to first and second hydraulic circuits 201 and 202. The first hydraulic flow path 211 may be branched into a second hydraulic flow path 212 and a third hydraulic flow path 213. The third hydraulic flow path 213 may be connected to the second hydraulic circuit 202. Therefore, the hydrau
Example
[0228]Hereinafter, an electric brake system 3 according to a third embodiment of will be described.
[0229]In the following description of the electric brake system 3 according to the third embodiment, except for an additional description with a different reference numeral, a description of the same parts as those shown in the electric brake systems 1 and 2 according to the first and second embodiment will be omitted to prevent duplication.
[0230]FIG. 13 is a hydraulic circuit diagram illustrating the electric brake system 3 according to the third embodiment.
[0231]Referring to FIG. 13, according to the third embodiment, a first hydraulic flow path 211 of the electric brake system 3 may connect a first pressure chamber 112 to first and second hydraulic circuits 201 and 202. The first hydraulic flow path 211 may be branched into a second hydraulic flow path 212 and a third hydraulic flow path 213. The third hydraulic flow path 213 may be connected to the second hydraulic circuit 202. Theref
PUM
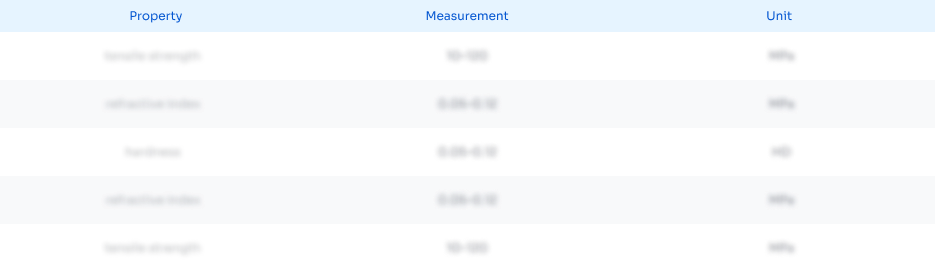
Abstract
Description
Claims
Application Information
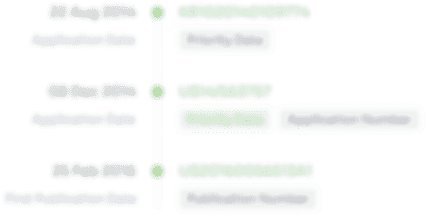
- R&D Engineer
- R&D Manager
- IP Professional
- Industry Leading Data Capabilities
- Powerful AI technology
- Patent DNA Extraction
Browse by: Latest US Patents, China's latest patents, Technical Efficacy Thesaurus, Application Domain, Technology Topic.
© 2024 PatSnap. All rights reserved.Legal|Privacy policy|Modern Slavery Act Transparency Statement|Sitemap