Electrical contact between electrically conducting polymer coated wires and electrically conducting substrates using wire bonding
- Summary
- Abstract
- Description
- Claims
- Application Information
AI Technical Summary
Benefits of technology
Problems solved by technology
Method used
Examples
Example
Example 1
[0383]Two holes are machined through a substrate. The holes are 3 mm apart, 250 μm in diameter, and are machined at an angle of 15° with respect to a first (upper) surface of the substrate. The surfaces confining the holes are electroless nickel immersion gold (ENIG) plated, thereby forming an electrical contact between the surfaces confining the holes and first conducting region.
[0384]A first positioning wire with a thickness of 200 μm is threaded through the two holes in the substrate in such a way that the first positioning wire forms a loop above the first surface of the substrate. The first positioning wire comprises an age hardened nickel-cobalt alloy. A distance D1 between the first positioning wire and the first conducting region is 230 μm. Furthermore, the first positioning wire is in electrical contact with the first conducting region. A conducting wire is placed between the first positioning wire and the first conducting region.
[0385]A second force of 5N is applied
Example
Example 2
[0386]Two opposite edges of a substrate is machined so that the edges slant by an angle of 3° with respect to a first (upper) surface of the substrate. A first conducting region partially covers the substrate, including both of the slanted edges.
[0387]A first end of a first positioning wire is resistance welded to the first slanted edge of substrate. The first positioning wire is in electrical contact with the first conducting region. Furthermore, the first positioning wire has a thickness of 200 μm. The first positioning wire comprises an age hardened nickel-cobalt alloy. A distance D1 between the first positioning wire and the first conducting region is 230 μm. A conducting wire is placed between the first positioning wire and the first conducting region. The first longitudinal portion is also placed 1.5 mm from the first slanted edge.
[0388]A second force of 5N is applied on a second end of the first positioning wire. The second force is used to bring the second end and the
Example
Example 3
[0389]A substrate is provided. A first positioning wire is placed parallel to the first conducting region so that the first positioning wire and the first conducting region touch each other. A first end of the first positioning wire is resistance welded to the first conducting region at a first connection point. The first positioning wire is in electrical contact with the first conducting region. Furthermore, the first positioning wire has a thickness of 200 μm. The first positioning wire comprises an age hardened nickel-cobalt alloy.
[0390]A first force of 5N is applied on a second end of the first positioning wire. This partially deforms the first positioning wire, thereby creating a distance D1 between the first positioning wire and the first conducting region that is 230 μm. A conducting wire is placed between the first positioning wire and the first conducting region.
[0391]The press tool is removed, and the first positioning wire tries to regain the shape it had prior to t
PUM
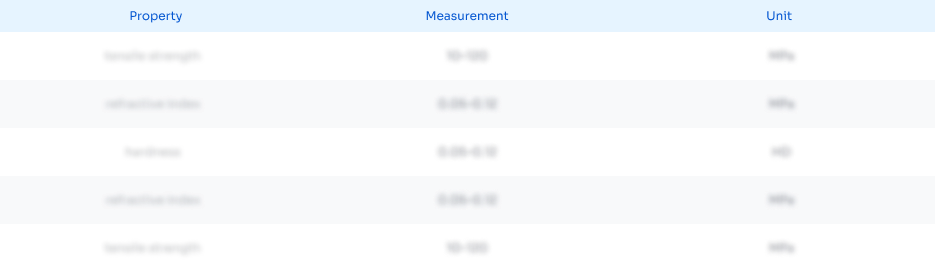
Abstract
Description
Claims
Application Information
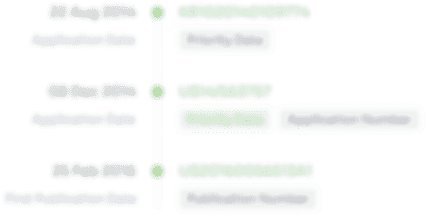
- R&D Engineer
- R&D Manager
- IP Professional
- Industry Leading Data Capabilities
- Powerful AI technology
- Patent DNA Extraction
Browse by: Latest US Patents, China's latest patents, Technical Efficacy Thesaurus, Application Domain, Technology Topic.
© 2024 PatSnap. All rights reserved.Legal|Privacy policy|Modern Slavery Act Transparency Statement|Sitemap