Injection molding machine and injection molding method
- Summary
- Abstract
- Description
- Claims
- Application Information
AI Technical Summary
Benefits of technology
Problems solved by technology
Method used
Image
Examples
Example
[0075]The injection molding machine 100 in the second embodiment of the disclosure is equipped with the porous plate 70 on the flow path of the melted resin in order to improve kneading property, and other configurations of the injection molding machine 100 are the same as those of the injection molding machine 1 of the first embodiment. Thus, elements having the same function and configuration are marked with the signs the same as those of the first embodiment, and descriptions thereof are omitted.
[0076]The porous plate 70 of the disclosure is a disk-shaped plate arranged on the flow path of the melted resin, and a number of pores 71a having predetermined diameters penetrating in a thickness direction are arranged in a center section 71. The porous plate 70 is arranged in a way of standing relative to a direction of the flow path of the melted resin to allow the melted resin to pass through the inside of the pores 71a. In the embodiment, the porous plate 70 is arranged between the inj
PUM
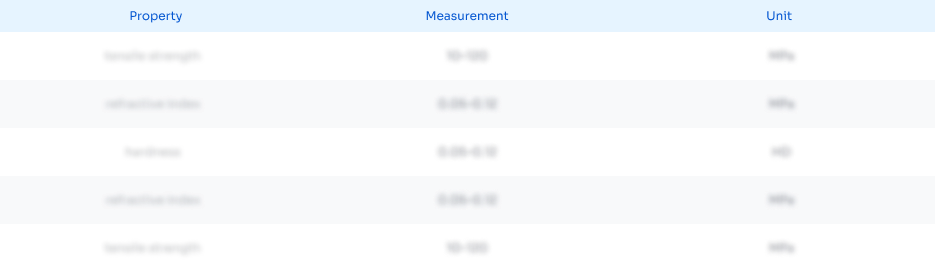
Abstract
Description
Claims
Application Information
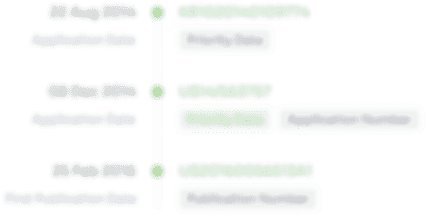
- R&D Engineer
- R&D Manager
- IP Professional
- Industry Leading Data Capabilities
- Powerful AI technology
- Patent DNA Extraction
Browse by: Latest US Patents, China's latest patents, Technical Efficacy Thesaurus, Application Domain, Technology Topic.
© 2024 PatSnap. All rights reserved.Legal|Privacy policy|Modern Slavery Act Transparency Statement|Sitemap