Chip-on-film use copper foil
- Summary
- Abstract
- Description
- Claims
- Application Information
AI Technical Summary
Benefits of technology
Problems solved by technology
Method used
Examples
Example
EXAMPLES 1 to 3
[0029]As the copper foil, electrodeposited copper foil (B-WS foil, made by Furukawa Circuit Foil) was used. This was formed on its surface with an alloy fine roughening particle layer by plating by a copper-cobalt-nickel alloy. The plating solution composition and plating conditions were as follows:
[0030]Cu:2g / literCo:8g / literNi:8g / literAmmonium sulfate:40g / literBoric acid:20g / literpH:3.5Temperature:40° C.Current density:15A / dm2
[0031]The inventors changed the plating times under the above conditions to obtain different alloy compositions on the surfaces of the COF copper foil. The results are shown in Table 1. In Table 1, the contents of the copper, cobalt, and nickel are shown in units of mg / dm2. The ratios with respect to the copper as 1 are shown in parentheses.
[0032]TABLE 1Content ofContent ofContent ofExamplecoppercobaltnickel17.8 (1)12.95 (1.66)11.35 (1.45) 26.6 (1)11.02 (1.67)9.44 (1.43)36.6 (1)10.95 (1.66)9.69 (1.47)
Example
EXAMPLE 4
[0033]As the copper foil, rolled copper foil (made by Nippon Foil Manufacturing Co., Ltd.) was used. This was formed on its surface with an alloy fine roughening particle layer by plating by a copper-cobalt-nickel alloy. The plating solution composition and plating conditions were as follows:
[0034]Cu:2g / literCo:8g / literNi:8g / literAmmonium sulfate:40g / literBoric acid:20g / literpH:3.5Temperature:40° C.Current density:15A / dm2
[0035]The alloy composition on the surface of the COF copper foil prepared under the above conditions is shown in Table 2. The inventors were able to obtain copper foil having a smooth surface of Rz: 0.50 and Ra: 0.06. In Table 2, the contents of the copper, cobalt, and nickel are shown in units of mg / dm2. The ratios with respect to the copper as 1 are shown in parentheses.
[0036]TABLE 2Content ofContent ofContent ofExamplecoppercobaltnickel46.5 (1)9.5 (1.46)7.5 (1.15)
[0037]The inventors bonded polyimide film made by a film maker A at a high tempe
PUM
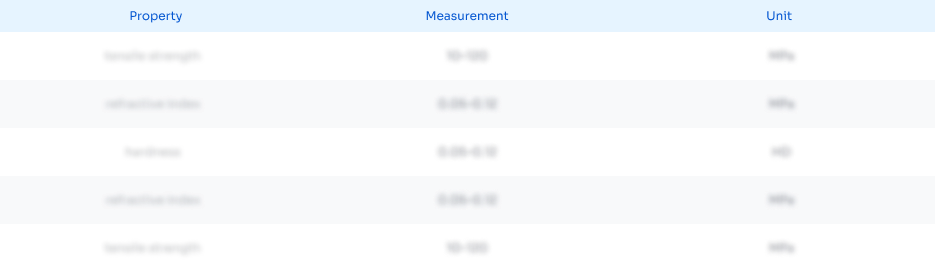
Abstract
Description
Claims
Application Information
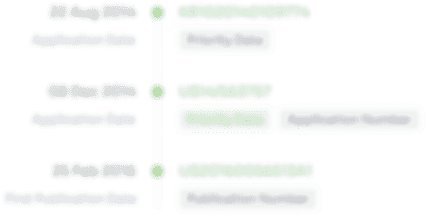
- R&D Engineer
- R&D Manager
- IP Professional
- Industry Leading Data Capabilities
- Powerful AI technology
- Patent DNA Extraction
Browse by: Latest US Patents, China's latest patents, Technical Efficacy Thesaurus, Application Domain, Technology Topic.
© 2024 PatSnap. All rights reserved.Legal|Privacy policy|Modern Slavery Act Transparency Statement|Sitemap