Taught position modification device
a position modification and position technology, applied in the direction of electric programme control, program control, instruments, etc., can solve the problems of requiring increased labor and time to correct the program, requiring a large amount of preparation of three-dimensional models, and requiring a considerable error in the program motion path, etc., to achieve the effect of short time and easy modification of the program
- Summary
- Abstract
- Description
- Claims
- Application Information
AI Technical Summary
Benefits of technology
Problems solved by technology
Method used
Image
Examples
Embodiment Construction
[0022]Referring to FIG. 1, a robot system according to an embodiment of this invention will be described.
[0023]The robot system includes a robot controller 1, and a robot 2 having robot arms, etc. serving as a movable portion of the robot. A visual sensor 4 such as a CCD camera is attached to a distal end of the robot arms. The robot controller 1 is connected to servomotors for driving the movable portion of the robot 2, and controls the servomotors to operate the robot. An information processing device (in this embodiment, a personal computer which will be referred to as PC) 5 and an offline programming system 6 are connected to the robot controller 1 via Ethernet (trademark) cables 7. A teaching pendant 3 is connected to the robot controller 1 via Ethernet (trademark) cables 7 or RS-422 cables.
[0024]In the case of Ethernet (trademark) cables being used for the connection, direct information exchange can be achieved between the teaching pendant 3, the PC 5, and the offline programming
PUM
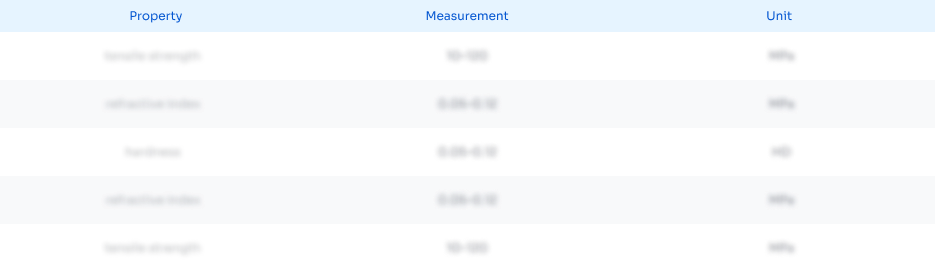
Abstract
Description
Claims
Application Information
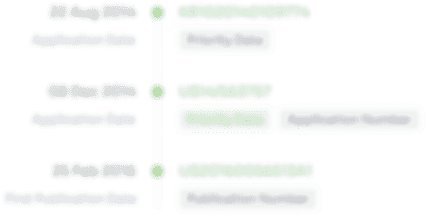
- R&D Engineer
- R&D Manager
- IP Professional
- Industry Leading Data Capabilities
- Powerful AI technology
- Patent DNA Extraction
Browse by: Latest US Patents, China's latest patents, Technical Efficacy Thesaurus, Application Domain, Technology Topic.
© 2024 PatSnap. All rights reserved.Legal|Privacy policy|Modern Slavery Act Transparency Statement|Sitemap