Shielding coating for selective metallization
- Summary
- Abstract
- Description
- Claims
- Application Information
AI Technical Summary
Benefits of technology
Problems solved by technology
Method used
Image
Examples
example 1
[0051]A plurality of polymer substrates chosen from ABS, PC / ABS (XANTAR™ 3720) and PC (XANTAR™ 3730) was provided. Each substrate was treated and selectively electroless copper plated according to the method disclosed in Table 1 below. Each polymer substrate was treated with a primer composition which included imidazole and one type of metal salt selected from manganese sulfate pentahydrate, nickel sulfate hexahydrate, zinc sulfate hexahydrate and copper nitrate or a primer composition which excluded a metal salt. Portions of the shielding coating where electroless copper plating was to take place were removed with silicon carbide type, P220 sandpaper. The aqueous ionic catalyst solution included 40 ppm palladium ions and 1,000 ppm 2,6-dimethylpyrazine. The reducing agent was dimethylamine borane at a concentration of 1 g / L. Electroless copper plating was done with CUPOSIT™ 71HS electroless copper bath available from Dow Advanced Materials.
[0052]
TABLE 1Process StepComponent and Con
example 2
[0056]The electroless copper plating method described in Example 1 above was repeated except that the heterocyclic nitrogen compound included in the primer composition was benzimidazole. All of the polymer substrates had bright copper deposits. The background plating results are disclosed in the table below.
[0057]
TABLE 3Metal Salt 0.01MABSPC / ABSPCManganese sulfateNo backgroundNo backgroundNo backgroundpentahydrateplatingplatingplating(2.1 g / L)Nickel sulfateNo backgroundNo backgroundNo backgroundhexahydrateplatingplatingplating(2.6 g / L)Zinc sulfateMinorNo backgroundNo backgroundhexahydratebackgroundplatingplating(2.7 g / L)platingCopper nitrateMinorNo backgroundNo background(1.9 g / L)backgroundplatingplatingplating—No backgroundNo backgroundNo backgroundplatingplatingplating
[0058]The benzimidazole provided good background plating inhibition with and without the metal salts. Only minor background plating was observed on the ABS polymer substrates where the metal salts were zinc su
example 3
[0059]The electroless copper plating method described in Example 1 above was repeated except that the heterocyclic nitrogen compound included in the primer composition was 2-phenyl-imidazole. All of the polymer substrates had bright copper deposits. The background plating results are disclosed in the table below.
[0060]
TABLE 4Metal Salt 0.01MABSPC / ABSPCManganese sulfateSignificantMinorMinorpentahydratebackgroundbackgroundbackground(2.1 g / L)platingplatingplatingNickel sulfateNo backgroundMinorMinorhexahydrateplatingbackgroundbackground(2.6 g / L)platingplatingZinc sulfateNo backgroundNo backgroundNo backgroundhexahydrateplatingplatingplating(2.7 g / L)Copper nitrateMinorNo backgroundNo background(1.9 g / L)backgroundplatingplatingplating—No backgroundNo backgroundNo backgroundplatingplatingplating
[0061]Best results were achieved when no metal salt was included in the primer composition and when the metal salt zinc sulfate pentahydrate was included. Copper nitrate also provided good b
PUM
Property | Measurement | Unit |
---|---|---|
Density | aaaaa | aaaaa |
Density | aaaaa | aaaaa |
Hydrophobicity | aaaaa | aaaaa |
Abstract
Description
Claims
Application Information
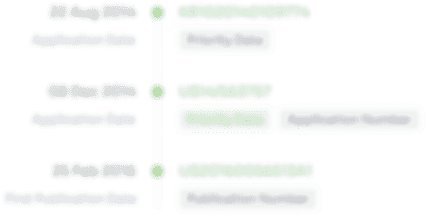
- R&D Engineer
- R&D Manager
- IP Professional
- Industry Leading Data Capabilities
- Powerful AI technology
- Patent DNA Extraction
Browse by: Latest US Patents, China's latest patents, Technical Efficacy Thesaurus, Application Domain, Technology Topic.
© 2024 PatSnap. All rights reserved.Legal|Privacy policy|Modern Slavery Act Transparency Statement|Sitemap