Method for making shoe-pad
A production method and technology for insole, which are applied in the directions of household components, applications, household appliances, etc., can solve problems such as discomfort, inconvenience in walking, sliding insole, etc., and achieve the effects of good strength, convenient production, and good anti-vibration.
- Summary
- Abstract
- Description
- Claims
- Application Information
AI Technical Summary
Benefits of technology
Problems solved by technology
Method used
Image
Examples
Embodiment 1
[0026] Embodiment 1, as shown in Fig. 1 to Fig. 8, the manufacturing method of the insole of the present embodiment, comprises the following steps successively:
[0027] 1. Raw materials and ingredients: select the insole surface cloth 12 as the raw material, the ingredients are component a and component b and place them separately, wherein the composition of component a is: polyether polyol 40%, polyester polyol 55%, Butylene Glycol or / and Ethylene Glycol or / and Propylene Glycol Neopentyl Glycol or / and Hexylene Glycol or / and Diethylene Glycol or / and Dipropylene Glycol 4.5%, Stannous Octylate or / and Dibutyltin Dilaurate or / and bismuth isooctanoate 0.5%; wherein the composition of component b is: polyether polyol 30%, polyester polyol or / and polycarbonate diol 19.6%, isocyanate 50%, adipoyl chloride or / and phosphoric acid or 0.1% of oleic acid, 0.3% of butanediol or / and neopentyl glycol or / and hexanediol, and the above are percentages by weight. The above
Embodiment 2
[0031] Embodiment 2, as shown in Fig. 1 to Fig. 8, the manufacturing method of the insole of the present embodiment comprises the following steps successively:
[0032] 1. Raw materials and ingredients: select the insole surface cloth 12 as the raw material, the ingredients are component a and component b and place them separately, wherein the composition of component a is: polyether polyol 60%, polyester polyol 37.5%, Butylene Glycol or / and Ethylene Glycol or / and Propylene Glycol Neopentyl Glycol or / and Hexylene Glycol or / and Diethylene Glycol or / and Dipropylene Glycol 2%, Stannous Octylate or / and Dibutyltin Dilaurate or / and bismuth isooctanoate 0.5%; wherein the composition of component b is: polyether polyol 41.9%, polyester polyol or / and polycarbonate diol 15%, isocyanate 40%, adipoyl chloride or / and phosphoric acid or 0.1% of oleic acid, 3% of butanediol or / and neopentyl glycol or / and hexanediol, and the above are percentages by weight.
[0033] 2. O
Embodiment 3
[0036] Embodiment three, as shown in Fig. 1 to Fig. 8, the manufacturing method of the insole of the present embodiment, comprises the following steps successively:
[0037] 1. Raw materials and ingredients: select the insole surface cloth 12 as the raw material, the ingredients are component a and component b and place them separately, wherein the composition of component a is: polyether polyol 38.5%, polyester polyol 55%, Butylene Glycol or / and Ethylene Glycol or / and Propylene Glycol Neopentyl Glycol or / and Hexylene Glycol or / and Diethylene Glycol or / and Dipropylene Glycol 5%, Stannous Octylate or / and Dibutyltin Dilaurate or / and bismuth isooctanoate 1.5%;
[0038] Wherein the composition of component b is: polyether polyol 50%, polyester polyol or / and polycarbonate diol 10%, isocyanate 38.9%, adipoyl chloride or / and phosphoric acid or oleic acid 0.1%, butanediol Or / and neopentyl glycol or / and 1% of hexanediol, and the above are percentages by weight.
PUM
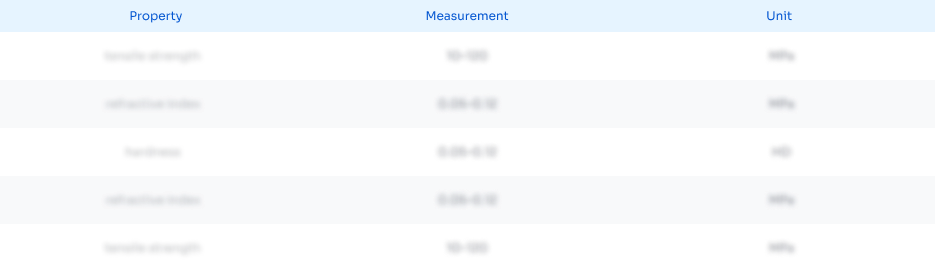
Abstract
Description
Claims
Application Information
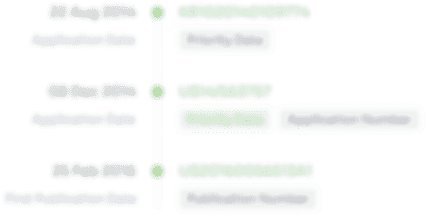
- R&D Engineer
- R&D Manager
- IP Professional
- Industry Leading Data Capabilities
- Powerful AI technology
- Patent DNA Extraction
Browse by: Latest US Patents, China's latest patents, Technical Efficacy Thesaurus, Application Domain, Technology Topic.
© 2024 PatSnap. All rights reserved.Legal|Privacy policy|Modern Slavery Act Transparency Statement|Sitemap