Glass suitable for chemically tempering and chemical tempered glass
A chemical tempering glass and chemical tempering technology, applied in glass production, glass tempering, glass manufacturing equipment and other directions, can solve the problems of difficult manufacturing process, difficult to eliminate bubbles, increase glass viscosity, etc. The effect of reducing the production temperature and improving the yield
- Summary
- Abstract
- Description
- Claims
- Application Information
AI Technical Summary
Benefits of technology
Problems solved by technology
Method used
Image
Examples
Embodiment Construction
[0024] Components that may be contained in the glass of the present invention will be described below, and the content of each component is expressed in % by weight.
[0025] SiO 2 It is the main component to form the glass skeleton. The higher its content, the more it can improve the chemical durability and the mechanical strength of the glass. When the content is below 55%, the chemical stability of the glass is not good, but when the content exceeds 61.5%, the melting temperature is too high. high. Therefore, SiO 2 The content is 55-61.5%.
[0026] Al 2 o 3 In the glass composition, it provides performance for the ion exchange of the glass surface, and is also a necessary component to improve the chemical stability of the glass, reduce the crystallization tendency of the glass, and improve the hardness and mechanical strength of the glass. If Al 2 o 3 When the content is less than 5%, the exchange effect is not good, and the chemical stability of the glass is not good; w
PUM
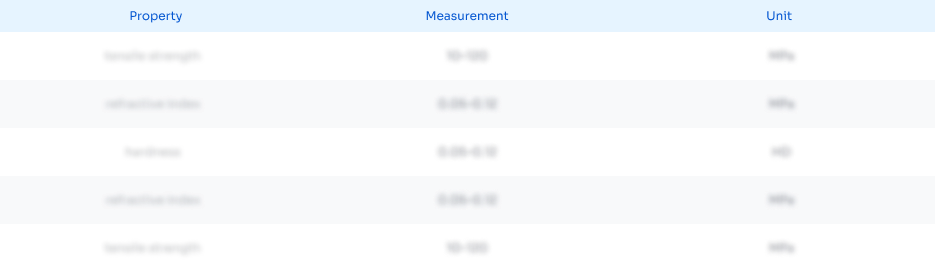
Abstract
Description
Claims
Application Information
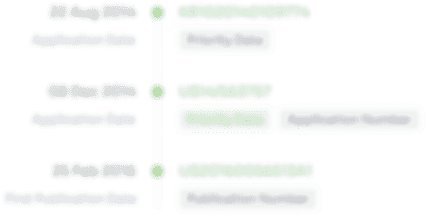
- R&D Engineer
- R&D Manager
- IP Professional
- Industry Leading Data Capabilities
- Powerful AI technology
- Patent DNA Extraction
Browse by: Latest US Patents, China's latest patents, Technical Efficacy Thesaurus, Application Domain, Technology Topic.
© 2024 PatSnap. All rights reserved.Legal|Privacy policy|Modern Slavery Act Transparency Statement|Sitemap