Surface treatment method of insert in vacuum casting and APG processes
A technology of vacuum casting and surface treatment, applied in the direction of epoxy resin glue, adhesive type, adhesive, etc., it can solve the problems of air leakage, gaps around the insulator inserts, inconsistent shrinkage rate, etc., and achieve the effect of preventing gaps
- Summary
- Abstract
- Description
- Claims
- Application Information
AI Technical Summary
Problems solved by technology
Method used
Examples
Embodiment Construction
[0015] Below in conjunction with specific embodiment the present invention is described in further detail:
[0016] Adhesive formulation; the adhesive formulation is: 100 parts of epoxy resin + 50 parts of phenolic resin + 175-200 parts of toluene + 175-200 parts of butanone, mixed and stirred for 2-2.5 hours at room temperature; adding diethyltetramethyl 1.5 parts of imidazole; stir at room temperature for 0.4-0.6 hours; add 8-10 parts of Qishi toughening agent and stir for 0.4-0.6 hours; stand still for 12-24 hours;
[0017] Insert cleaning;
[0018] dry;
[0019] Sealing parts: use scotch tape to seal the uncoated part according to the drawing requirements, and tear it off after the adhesive is cured;
[0020] Apply the glue 2-4 times at room temperature, dry the previous one and then apply the next one;
[0021] Preheat the glued insert, the preheating temperature is 135°C-145°C, and the time is 1-1.5 hours;
[0022] Take it out and keep it covered for later use.
[0023
PUM
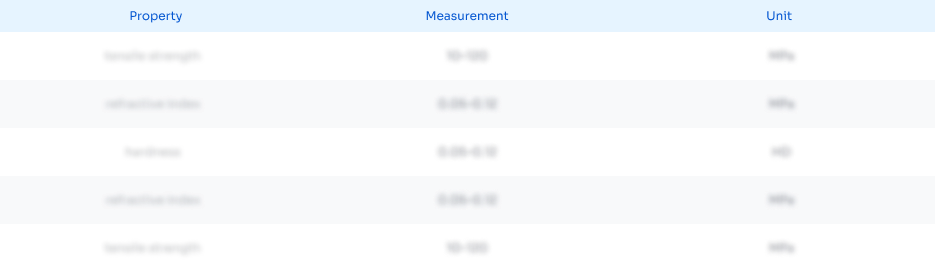
Abstract
Description
Claims
Application Information
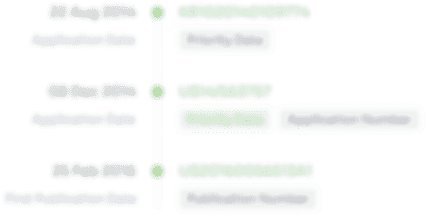
- R&D Engineer
- R&D Manager
- IP Professional
- Industry Leading Data Capabilities
- Powerful AI technology
- Patent DNA Extraction
Browse by: Latest US Patents, China's latest patents, Technical Efficacy Thesaurus, Application Domain, Technology Topic.
© 2024 PatSnap. All rights reserved.Legal|Privacy policy|Modern Slavery Act Transparency Statement|Sitemap