Main bearing block of low-speed diesel engine
A main bearing seat, bearing seat technology, applied in the direction of bearing components, shafts and bearings, rigid brackets of bearing components, etc., can solve the problem of prolonging the manufacturing cycle, warping deformation, mismatch between the thickness of the wings on both sides and the ratio of length and width, etc. problems, to achieve good control of deformation, reduce width, reduce the possibility of deformation and casting defects
- Summary
- Abstract
- Description
- Claims
- Application Information
AI Technical Summary
Problems solved by technology
Method used
Image
Examples
Embodiment Construction
[0012] See Figure 3 to Figure 4 , a main bearing seat of a low-speed diesel engine, comprising a bearing seat 1 and wing plates 2 on both sides of the bearing seat, characterized in that a welding structure is adopted between the bearing seat 1 and the wing plates 2 on both sides of the bearing seat. Bearing seat 1 is made of casting, and wing plate 2 is made of steel plate, and double-sided grooves are opened on the steel plate during welding. The width of the wing plates on both sides of the bearing seat does not exceed the radial edge of the bearing seat. Since the width of the wing plate is greatly reduced, it can be 300mm in production. The overall width of the main bearing housing has also been significantly reduced.
[0013] Apparently, the above-mentioned embodiments of the present invention are only examples for clearly illustrating the present invention, rather than limiting the implementation of the present invention. For those of ordinary skill in the art, other c
PUM
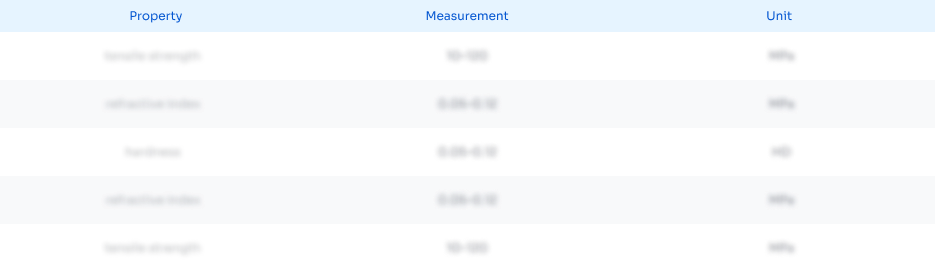
Abstract
Description
Claims
Application Information
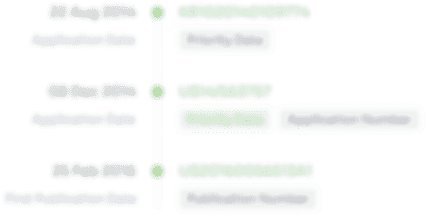
- R&D Engineer
- R&D Manager
- IP Professional
- Industry Leading Data Capabilities
- Powerful AI technology
- Patent DNA Extraction
Browse by: Latest US Patents, China's latest patents, Technical Efficacy Thesaurus, Application Domain, Technology Topic.
© 2024 PatSnap. All rights reserved.Legal|Privacy policy|Modern Slavery Act Transparency Statement|Sitemap